Revista Controle & Instrumentação – Edição nº 275 – 2022
|
|
¤
Cover Page
|
|

|
|
|
|
|
|
Estudar e gerenciar os metais, em todo seu ciclo de transformação, é papel da metalurgia, uma das mais antigas atividades do homem, que ainda perdura, acompanhando e impulsionando a evolução e o bem-estar da sociedade.
A história dessa atividade, em âmbito global, nos tempos mais recentes, pode ser facilmente resumida em dois fatos: os primeiros altos-fornos apareceram no século XIII, e a indústria metalúrgica contribuiu de forma essencial para a Revolução Industrial, no século XVIII.
Especificamente no Brasil, a metalurgia é atividade econômica de destaque, ao ponto de situar o país entre os dez maiores produtores mundiais, mais especificamente, ocupando a 9ª posição no ranking de produtores de aço, tendo produzido, em junho de 2022, de acordo com dados da World Steel Association, 2,9 megatoneladas de aço. Além disso, diferenciase de outros países, inclusive dos que estão à frente na tabela, no ponto questão ambiental, e a redução das emissões de carbono, graças à rota do carvão vegetal biorredutor.
A cada dia mais, as plantas industriais das metalúrgicas incorporam tecnologias de automação, computação em nuvem, robótica avançada e colaborativa, IIoT, big data, gêmeos digitais e simuladores, segurança da informação ou cybersecurity, machine learning, inteligência artificial, realidade aumentada, entre outras tecnologias potencializadoras e capacitadoras, que digitalizam e integram o chão-de-fábrica e o pensamento estratégico da organização, elevando seu patamar produtivo, e habilitando a metalurgia à Indústria 4.0. |
|
<
 |
Para dar uma ideia dos ganhos proporcionados, Cristiano de Lanna – coordenador do Grupo de Automação e TI da Associação Brasileira de Metais (ABM), e gerente Corporativo de Sistemas da Usiminas – cita estimativa da McKinsey: até 2025, os processos relacionados à Indústria 4.0 poderão reduzir custos de manutenção de equipamentos, entre 10% e 40%; reduzir o consumo de energia, entre 10% e 20%; e aumentar a eficiência do trabalho, entre 10% e 25%. |
|
|
|
Cientes dos benefícios, a siderurgia e a metalurgia têm investido e se beneficiado das oportunidades ofertadas pelas tecnologias da Indústria 4.0, em toda a cadeia produtiva. O período de 2020 a 2022 vem caracterizando-se por uma aceleração na procura dessas soluções, e a cultura está disseminando-se mais rapidamente, garantem os profissionais que atuam em automação de processos. |
|
|
 |
Nota-se, ainda, crescimento no número das empresas de automação, robótica e inteligência artificial, dedicadas a esses setores. Entre elas, a BM Group Polytec, cujo gerente Comercial, Rafael Lourenzo Jacob, confirma: “O nível de investimento em automação e robótica na metalurgia está em rápido crescimento, nos últimos anos, e, junto com elas, as tecnologias como IoT, big data e gêmeos digitais acabam ganhando espaço”. |
|
|
|
A defasagem percebida entre as indústrias metalúrgicas e as de outros segmentos do setor de bens de capital mecânico, na opinião de Jacob, tem causas diversas: “A indústria metalúrgica está passando por um momento semelhante ao que a automotiva passou há muitos anos, especialmente na área da robótica, impulsionada pela necessidade de aumento na segurança e ergonomia. Esse lapso de tempo pode ser explicado por motivos, como o grau de hostilidade e risco desses ambientes, pelo modelo de produção – que em partes não é contínuo – e pelas enormes dimensões e pesos envolvidos. Mas, à medida que essas tecnologias ficaram mais robustas, a aplicação na metalurgia se tornou possível, e, com o aumento de sua flexibilidade e número de funções, o retorno do investimento passou a ser atrativo”. |
|
 |
Segundo Marco Tanaka – vice-coordenador do Grupo de Trabalho de Manufatura Avançada da ABIMAQ (GTMAV), as soluções estão cada vez mais acessíveis, favorecendo o desenvolvimento de projetos adequados, inclusive, às necessidades de pequenas e médias indústrias. “Principalmente com relação a indústrias de pequeno porte, inclusive metalúrgicas, há um grande desafio a ser vencido, relacionado especialmente ao gap entre o que precisa e a realidade dessas empresas, pois, as máquinas precisam estar prontas para os dispositivos capturarem informações”, comenta Tanaka. |
|
|
|
Entre os motivos para esse crescimento de mercado, Tanaka lista a sobrevivência, como um dos principais motores da automação das metalúrgicas e das indústrias em geral: “Há cerca de dez anos, as empresas não se preocupavam com aumentos de preços de insumos, transporte, matéria-prima, etc., nem com produtividade, pois, repassavam os custos para o cliente. Hoje não dá mais. Para ser competitiva, é fundamental no mínimo monitorar as máquinas”.
No entanto, mesmo com o mercado se desenvolvendo, o nível de automação das linhas de produção de metalúrgicas ainda pode ser considerado baixo, se comparado às grandes indústrias alimentícias, farmacêuticas ou automotivas, “mas, essa realidade vem mudando muito rapidamente. Os grandes players já têm partes do processo totalmente automatizados há algum tempo, como o lingotamento contínuo ou processo de laminação nas siderúrgicas. Contudo, o mesmo não acontece com outras partes do processo, frequentemente muito dependentes da intervenção do ser humano, tais como amostragem, testes de qualidade, adições de matéria-prima, soldas”. |
|
 |
Para permanecerem competitivas, as indústrias em geral “necessitam de dados do fluxo de trabalho diário da operação e da manutenção desses dispositivos habilitados para internet”, detalha Murilo Pruano – da Braincube – e cita as plataformas de IIoT como opção para a democratização de dados, ou seja, favorecer que todos tenham acesso aos dados da fábrica: “Esse conceito está mudando os contornos da indústria, especialmente à medida que mais e mais máquinas inteligentes se juntam à frota. Usar dados no fluxo de trabalho diário é uma necessidade, na operação e na manutenção desses dispositivos habilitados para internet”. |
|
|
|
O casamento entre automação de processos e melhor aproveitamento dos recursos disponíveis é apontado por Lanna como um “dos principais benefícios das tecnologias disruptivas na siderurgia. Na mesma linha, há uma correlação linear com a melhoria dos processos e produtos”. Agrega, ainda, a melhora nas condições de trabalho em “partes do processo que expõem os operadores ao metal em alta temperatura ou movimentação de cargas muito pesadas, onde agora estão sendo inseridos os robôs de grande porte. Atividades de amostragens e medições de temperatura do metal líquido durante o refino, reparo do revestimento refratário dos fornos, movimentação de válvulas refratárias, adição de pó fluxante no lingotamento contínuo, e outras. Também está ocorrendo evolução na automação e controle de motores que são aplicados em diversas partes do processo, cuja atualização promove mais precisão e eficiência energética”, comenta Lanna.
As tecnologias aplicadas e a forma de interligação entre os sistemas de gestão e automação no setor metalúrgico e siderúrgico “não mudam muito quando comparado a outras indústrias. A interligação entre os sistemas é feita pelos protocolos-padrão de comunicação – Profibus-DP, Profinet e Ethernet IP nos níveis de campo e controle, e normalmente TCP/IP, no gerenciamento e planejamento”. Mas aqui também há novidades. De acordo com o coordenador do Grupo de Automação e TI da ABM, “já existe quem impulsione a aplicação do OPC-UA como protocolo universal também nessas indústrias, mas sua aplicação ainda não é muito difundida”. Lanna assegura que, “tendo os dados de processo chegado ao nível de gerenciamento, fica a cargo dos sistemas de TI criarem uma arquitetura de cloud computing, caso o produtor tenha interesse em utilizar o grande poder de processamento dos servidores de empresas como Amazon, Google ou Microsoft. Mas, hoje em dia, ainda é mais comum que o processamento digital ocorra em servidores internos, por cuidados em relação à segurança dos dados”.
O maior desafio encontrado pelas empresas especializadas em fazer a migração do ambiente usual para o da Indústria 4.0 tem o centro de usinagem como principal gargalo. Quanto menor a empresa, mais antigas são essas máquinas, exigindo às vezes um retrofit.
“O setor de metalurgia conta com muitas indústrias de pequeno porte, ainda com processos 100% dependentes do operador, e naquelas em que há centros de usinagem; essas máquinas são antigas, sem nenhum nível de automação”, declara o vice-coordenador do GTMAV da ABIMAQ, agregando outra dificuldade: muitos são centros de usinagens fechados, com tecnologia proprietária, e a idade média do parque instalado é de dez anos.
A Açovisa, antes da Pandemia, desenhara um plano 4.0 para aumento da produtividade e da interação com a equipe de vendas e qualidade. A empresa está toda alinhada e tradicionalmente investe em TIC para processos e qualidade, interligando as áreas, e também nos prazos de atendimento. Retomando um plano de investimentos de antes da Pandemia, a empresa, além de investir em software de gestão (SAP) – pois, sem ele, não é possível gerenciar os dados, e disponibilizar informações aos pontos de vendas, e, além disso, produzir dados para evitar desperdícios de matérias-primas e de insumos – também direcionou recursos para laboratório de ensaios de qualidade – equipamentos e mão-de-obra. Está realizando a substituição das máquinas-ferramenta e a adaptação de alguns equipamentos, renovando o parque, e investindo na qualidade do processo, com máquinas de corte a laser. Dessa forma, atingiu 50% de automação da planta e, até 2024, deve automatizar o restante – o que inclui investimentos em ferramentas para a área de vendas e de relacionamento com o mercado.
A ideia dessa indústria metalúrgica de médio porte, detentora de parque industrial com mais de 50 equipamentos em transformação, é trocar cerca de 30 máquinas, recapacitar as demais e, no longo prazo, substituir mais 60% das máquinas, automatizando e digitalizando toda a fábrica. O cronograma em andamento prevê que Açovisa chegue a 2025 nos padrões da Indústria 4.0.
A empresa reconhece que, na implementação de tecnologias relacionadas à Indústria 4.0, a metalurgia vem caminhando mais lentamente, mas prevê que o ritmo deva ser acelerado, porque essa indústria “precisa de uma planta verde, que gaste menos energia, economizando água, usando menos óleo solúvel e ferramentas de corte. Neste caso, a meta é atingir o mesmo nível dos setores que estão à frente. Esse é um processo de melhoria, contínuo e sem retorno à condição anterior”.
Esse caminho trilhado atende o que preceitua Tanaka, ao descrever o passo a passo. “Tudo começa no planejamento de como vai ser feita a jornada para poder relacionar os dados. Comece monitorando o gargalo e, aos poucos, aumente a abrangência do monitoramento, pois, assim, dará para ter ideia do payback, e comprovar os benefícios, que são imediatos”.
Fundamental também é a conscientização, desde a alta direção da indústria, de que a adoção de novas tecnologias pode contribuir para tornar a produção mais eficiente, com redução do uso de recursos naturais, geração de resíduos e consumo de energia.
As tecnologias para a indústria ajudam significativamente a implementação de uma economia sustentável, que tenha o desenvolvimento social entre seus objetivos. É aqui que entra a relação entre as políticas dessas empresas e o ESG (Environmental, Social, Governance). |
|
 |
|
Rafael Jacob afirma que a tecnologia e a automação contribuem para o ESG, no que diz respeito à segurança e ao meio ambiente: “Além da redução dos riscos, os sistemas automatizados são mais precisos e eficientes, trazendo grandes reduções no consumo de energia e nas emissões carbono para o meio ambiente. Um exemplo muito impactante é na fusão e no refino primário do aço, tanto em fornos elétricos, quanto em conversores LD, uma pequena redução de tempo ou perda de eficiência térmica reduz altamente o uso das fontes de energia e emissões de CO e CO2 ”.
E, entre as tecnologias 4.0, a aplicação do Gêmeo Digital permeia toda a produção, permitindo monitorar, testar ou fazer melhorias nos processos. Murilo cita o acompanhamento de um lote de lingotes de aço na fornalha: “O gêmeo digital leva em consideração cada variável, e pode dizer distintamente o que está em cada lote. Ao saber quais fatores têm mais influência no processo, as equipes podem melhor descrever os acontecimentos durante a produção. Isso pode ajudar, repetindo as melhores receitas várias vezes, o que leva à redução de custo, risco e desperdício. Se um engenheiro utiliza o desvio padrão em certo tipo de análise, é possível ver, na mesma linha do tempo, o desvio padrão da primeira e da última parte do processo; em processos de produção contínuos, possibilita a visualização dos dados de diferentes fontes ou sistemas, ao mesmo tempo. Também torna possível compreender como os parâmetros do processo funcionam e ajustá-los, afinal, algumas partes do processo de produção do aço levam milissegundos. Desse modo, disponibiliza ao gestor a informação certa, e ajuda a compreender as variáveis importantes que impactam o processo de produção”.
Inexiste um indicador específico da metalurgia, mas quem atua no setor confirma investimentos crescentes, que mostram contraponto importante: grande parte das empresas – 43% segundo pesquisa da ABDI – Agência Brasileira de Desenvolvimento Industrial – não identificam tecnologias digitais como fatores impulsionadores da indústria.
A percepção dos entrevistados é comprovada, por exemplo, pela ABDI, que, em conjunto com a Fundação Getúlio Vargas (FGV), trimestralmente levanta informações sobre a digitalização das empresas brasileiras, com o objetivo de monitorar, principalmente, a jornada das MPEs rumo à economia digital, para identificar tendências para o curto e médio prazos.
A Sondagem Especial Indústria 4.0: Cinco Anos Depois, lançada em abril de 2022, pela CNI – Confederação Nacional da Indústria – informa crescimento significativo frente aos resultados da primeira edição desse levantamento, realizado em 2016, quando apenas 48% utilizam alguma tecnologia relacionada à Indústria 4.0. Neste último relatório, sete em cada dez empresas no Brasil fazem uso de pelo menos uma tecnologia digital, mas, quando inqueridos sobre quais são utilizadas, seguem sendo as mais utilizadas, as que proporcionam melhorias no processo produtivo. |
|
 |
|
O mercado parece inesgotável, assim como os ganhos possibilitados: a Global Industry Analysts Inc. (GIA) estimava o mercado global da Indústria 4.0 em US$ 90,6 bilhões, em 2020, devendo chegar a US$ 219,8 bilhões, até 2026. Já a ABDI, em 2020, calculou que, com a adoção da indústria 4.0, o país pode reduzir os custos industriais em, no mínimo, R$ 73 bilhões, por ano. A segunda Sondagem Trimestral sobre Transformação Digital nas empresas brasileiras, divulgada em agosto, com dados coletados em junho deste ano, mostrou crescimento em empresas de todos os portes. No caso específico da indústria, o indicador de investimentos em digitalização evoluiu, de 20,4%, para 25%.
Parece promissor, e as empresas de automação têm capacitação e tecnologia em níveis internacionais, para atender a indústria. “No entanto, se a demanda crescer muito rapidamente, faltará braço, principalmente na programação da máquina”, constata Tanaka, ao informar que vem crescendo, no mercado, a disponibilidade de “plataformas que simplificam a programação pelo operador no chão-de-fábrica. Pelo lado da integradora, a dificuldade com profissionais para o corpo de engenharia também é presente. Há poucos formados nessa área, seja em nível técnico, seja no âmbito do ensino superior”.
As plataformas de IIoT – garante Pruano – facilitam a qualificação dos líderes industriais de amanhã, para que a manufatura possa florescer: “Elas são usadas para capacitar as equipes humanas, e não para substituir seres humanos por máquinas automatizadas. Assim, os profissionais podem contribuir de maneira eficaz para a missão da empresa. As plataformas de IIoT são ferramentas que ampliam a capacidade de trabalho dos funcionários, favorecendo que trabalhem melhor, mais rápido e com mais facilidade. Elas promovem uma comunidade de pensadores, altamente qualificados e engajados, leais à empresa, e focados em levá-la adiante”. |
|
 |
|
Como parte de um novo ciclo de crescimento sustentável da companhia, a Gerdau deu início às operações do novo lingotamento contínuo de blocos e tarugos da Usina de Pindamonhangaba/SP. O equipamento permite à Gerdau um processo mais automatizado e com melhor rendimento, resultando na entrega de produtos diferenciados, e em um patamar ainda mais elevado de qualidade para os mercados demandantes. A atualização tecnológica da unidade está alinhada às perspectivas futuras de aumento da matriz de veículos elétricos e híbridos no Brasil. Com o novo lingotamento, a Usina de Pindamonhangaba da Gerdau ganha um novo patamar de competitividade e modernidade – com investimento de aproximadamente R$ 700 milhões, o equipamento traz ganhos em três frentes: segurança, pois, trata-se de um equipamento mais automatizado e moderno; qualidade, pois, o novo lingotamento possibilita a produção de aços “clean steel”, cuja tecnologia dá ao produto mais limpeza e maior resistência, aumentando sua vida útil, buscando atender a demanda da indústria automobilística por automóveis mais leves; e competitividade, pois, o novo equipamento possibilita uma redução de custos e o aumento de produtividade da operação. |
|
 |
“Temos realizado investimentos em nossas usinas de aços especiais, para aumentar a produtividade e atender as necessidades e a demanda crescente dos nossos clientes. O novo lingotamento da Usina de Pindamonhangaba está alinhado aos conceitos de indústria 4.0 e aumentará a qualidade e competividade das nossas operações nesse segmento. A inauguração desse equipamento, bem como nosso plano de modernização das operações até 2025, reforçam nossa presença nos mercados em que atuamos, bem como nossa visão otimista para o setor automotivo brasileiro, que deve, nos médio e longo prazos, ter seus níveis de produção recuperados”, afirma Rubens Pereira, vice-presidente de Aços Especiais da Gerdau no Brasil. |
|
|
|
A Gerdau está planejando um ciclo de modernização e manutenção de suas operações de aços especiais no Brasil, até 2025. Dentro desse plano, que ainda depende de aprovações do conselho de administração da empresa, estão investimentos em manutenção das operações, e na atualização tecnológica, ambiental e modernização. E esse plano está dividido entre as três usinas de aços especiais no Brasil: Mogi das Cruzes/ SP, Pindamonhangaba/SP e Charqueadas/RS, sendo que aproximadamente 60% desses investimentos serão para as plantas do Estado de São Paulo, e 40% para a operação no Rio Grande do Sul. |
|
 |
“Esse movimento no segmento de aços especiais é resultado da preparação da Gerdau para um novo ciclo de crescimento futuro, com foco nas Américas, com o objetivo de gerar mais valor para seus clientes, e ser uma organização ainda mais sustentável. Reforçamos ainda nosso otimismo com a evolução do segmento automobilístico, e estamos acompanhando na Gerdau a evolução da demanda e da transformação tecnológica dessa indústria. Nos últimos anos, a empresa passou por uma profunda transformação cultural e digital, que a tornou ainda mais focada em pessoas, mais digital, inovadora, diversa e inclusiva”, comenta Gustavo Werneck, CEO da Gerdau. |
|
|
|
 |
|
Além do novo lingotamento contínuo da Usina de Pindamonhangaba, outros investimentos em aços especiais entraram em operação recentemente, dentro do plano de R$ 1 bilhão de investimentos, anunciados em 2021: nesse ano, a planta de Mogi das Cruzes teve sua aciaria reativada; na usina gaúcha de Charqueadas foi instalado um novo forno de recozimento e esferoidização de barras de aço, o qual traz maior qualidade e produtividade ao processo produtivo, ganhos de competitividade e novos conceitos de segurança das pessoas. Esta atualização tecnológica também permitirá à Gerdau atender à demanda crescente por materiais com tratamentos térmicos complexos, principalmente do setor automotivo, uma vez que há um aumento de capacidade instalada para este processo.
Mas, a Gerdau vem trabalhando sua modernização há algum tempo baseada em quatro pilares: indústria 4.0, segurança 4.0, perspectiva do cliente e supply chain integrado. Em todos eles, há uso intensivo de dados, e um trabalho respaldado pela metodologia ágil. A empresa fez uso de modelagens matemáticas, Python, data lake, nuvem, e passou a usar tecnologias como machine learning e Inteligência artificial, para aumentar o impacto dos bons resultados, alcançados de maneira cuidadosa.
Uma das técnicas que a Gerdau usa é o video analytics, a partir de câmeras no pátio de sucatas, que registram a movimentação das pessoas, e alertam caso haja alguém em área de risco. O uso de equipamentos de proteção (EPIs) também é monitorado pelo sistema, que faz a identificação da imagem e conta com machine learning, para assinalar quando existem situações de não conformidade.
E o cabedal de conhecimento e tecnologia aparece em vários pontos dos trabalhos, como modelos de otimização do consumo de ligas nos fornos de aciaria, para redução do consumo de combustível nas áreas fabris e para o consumo de gás para laminação.
A Gerdau faz uso da tecnologia IoT em cerca de 900 ativos, equipamentos conectados, usando sensores inteligentes, que coletam dados que são analisados e usados, por exemplo, na manutenção preditiva. E, desde 2020, a Gerdau trabalha com o gêmeo digital, usando dados reais para simular diferentes cenários de fabricação e projeções. A adoção de gêmeo digital já está bem consolidada na usina Ouro Branco, em Minas Gerais, a maior da empresa no mundo, com capacidade de 4,5 milhões de toneladas de aço bruto/ano. A aciaria foi a área escolhida para começar a usar a tecnologia, mas a ideia é escalar o gêmeo digital na planta de Ouro Braco, enquanto, em outras plantas, o conceito está sendo trabalhado em menor escala.
A usina de Ouro Branco também está liderando a implementação de uma rede privativa dedicada 5G e Long Term Evolution (LTE) 4G, criando uma rede de transporte (backbone) de TI. Esse projeto, dividido em três fases, que a Gerdau firmou com a Claro/Embratel, prevê a instalação de torres no local, para ampliar a abrangência da conectividade e as possibilidades de automação, com cobertura em mais de 8,3 milhões de m².
No início, será instalada uma rede privativa LTE 4G, com capacidade total de 256 Mbps. Já nessa etapa, a área coberta deve ser maior do que a atual, possibilitando o aumento da abrangência das iniciativas da Indústria 4.0 já adotadas na unidade. Na segunda fase, será implantado o 5G, na frequência 3.5 GHz, e aplicações críticas não terão infraestrutura compartilhada com a rede pública. Somando as duas frequências, a planta passará a ter uma capacidade de 3,8 Gbps. A terceira etapa envolverá o adensamento da rede privativa LTE 4G e 5G, para fornecer mais capacidade combinada, chegando a 4,8 Gbps, e ampliar a cobertura para toda a extensão operacional da planta.
Cada máquina conectada receberá um SIMCard exclusivo para acessar a rede. Com isso, a autenticação do equipamento será automática, sem a necessidade do uso de senhas para conexão. Suportada pela rede e backbone de TI instalados, a Gerdau pretende ampliar seus investimentos em tecnologias como veículos autônomos e telecontrolados, além de gêmeos digitais, Internet das Coisas e Inteligência Artificial. |
|
 |
“Em um cenário cada vez mais competitivo no setor, que exige uma busca contínua por mais excelência operacional, a transformação digital se torna crucial, para evolução em produtividade, segurança das pessoas e gestão sistêmica da nossa operação”, afirma Rafael Gambôa, diretor da Usina de Ouro Branco. |
|
|
|
A ideia é possibilitar a ampliação do gerenciamento e sensoriamento de ativos críticos, uso de carboxímetros conectados, caminhões autônomos, retroescavadeiras telecontroladas, além da monitoração inteligente por câmeras e drones para segurança preditiva.
Com 35 anos de operação, a usina de Ouro Branco tem capacidade 3,9 milhões de toneladas de aço bruto, por ano, em uma planta de 10 milhões de m², com mais de 7 mil colaboradores.
A unidade possui um centro de monitoramento para os principais ativos e equipamentos estratégicos para a operação das usinas no Brasil, utilizando modelos de inteligência artificial de forma preditiva, antecipando possíveis problemas que venham a ocorrer.
Neste cenário, a nova rede privativa também deverá apoiar as ações desenvolvidas pelo centro, fornecendo mais disponibilidade e abrangência para o monitoramento. |
|
|
|
|
LEIA MAIS
NA EDIÇÃO IMPRESSA |
|
DESEJANDO
MAIS INFORMAÇÕES: redacao@editoravalete.com.br
|
|
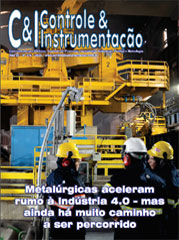 |
Clique na capa da revista para
ler a edição na íntegra |
|
|