Revista Controle & Instrumentação Edição nº 259 2020
|
|
¤
Cover Page
|
|
 |
|
|
|
|
|
 |
|
Oano de 2020 está sendo apontado, por analistas
e estudiosos, como um marco na digitalização
das indústrias, em resposta aos problemas e às
dificuldades geradas pela pandemia do novo coronavírus.
De forma semelhante, especialistas em automação
industrial garantem que o protocolo OPC UA (Open Platform
Communications – Unified Architecture) tornase
cada dia mais essencial, quando o assunto
é digitalização industrial e Indústria 4.0, por
favorecer a integração do chão-de-fábrica e
dos ambientes corporativos. |
|
 |
Peter Lutz, diretor de Field Level Communications,
da OPC Foundation, conta
que o OPC UA foi introduzido em 2008, e
é uma tecnologia de comunicação industrial
bem estabelecida para interoperabilidade entre
fornecedores e aplicativos de software, com base em
uma estrutura industrial comum (IEC62541). A estrutura
do OPC UA consiste em um protocolo de camada superior,
recursos de modelagem de informações e mecanismos
de segurança integrados. Ele é usado hoje em uma
ampla variedade de casos em Automação de Fábrica e
Processos. O OPC UA está sendo combinado com tecnologias
e padrões complementares, para cumprir
a promessa de uma solução de comunicação
unificada e baseada em padrões. Exemplos
de tais tecnologias complementares são, por
exemplo, Ethernet, Ethernet APL e Ethernet
TSN (IEEE 802.3 e IEEE 802.1), bem como
protocolos de camada superior, como UDP
/ IP, TCP / IP ou MQTT. No futuro, o OPC UA
se estenderá ao nível de campo, para que uma
Digitalização
e OPC UA:
Controle & Instrumentação Nº 259 | 2020 35
solução de comunicação IIoT consistente e unificada seja
disponibilizada, fornecendo conectividade e interconectividade,
ponta a ponta, do campo à nuvem, e vice-versa,
cobrindo todos os requisitos para automação industrial,
como em tempo real, segurança funcional, e controle de
movimento. |
|
|
|
|
 |
Como afirma Marcio Santos – Technical Consultant da Siemens
Infraestrutura e Indústria,
e diretor Técnico da tecnologia
Profinet, pela Associação
Profibus & Profinet Brasil – o
OPC UA será “um grande divisor
de águas ao pavimentar o caminho
que integrará as comunicações
industriais convergentes, envolvendo o
chão-de-fábrica e os ambientes corporativos, sejam eles
on premise (local), ou na nuvem”. |
|
|
|
Quase todos os controladores de todos os fabricantes
de automação fornecem conectividade OPC UA para
a diversidade de aplicativos de TI e OT (como sistemas
SCADA, HMI, MES / ERP), e até mesmo sistemas de ponta,
ou em nuvem. No entanto, os dispositivos de campo,
normalmente, são conectados por meio de vários barramentos
de campo e, portanto, ainda não fornecem conectividade
OPC UA de forma direta. Logo, os gateways
e/ou controladores são normalmente usados para integrar
ou agregar dados, e disponibilizar esses dados no OPC
UA. |
|
 |
Ao definir esse protocolo
como “um catalisador do caminho
da quarta revolução
industrial”, Cesar Cassiolato – presidente e CEO da Vivace
Process Instruments – comenta
que o OPC UA constitui a
solução mais atual que usualmente
vem sendo implementada
nas indústrias, com o intuito de garantira conexão entre os diversos dispositivos do chão-de-fábrica.
Nesse universo, conceitos como comunicação independente
de plataforma e fornecedor, segurança de
dados, padronização e inteligência descentralizadas são
temas correlatos. |
|
|
|
 |
Para outros, como Pedro
Vieira – gerente Setorial de Gestão
de Dados de Engenharia na
Petrobras –, a importância do
OPC UA vincula-se ao fato
de ser um protocolo aberto,
independente do OLE (Object
Linking and Embedding),
que unifica os demais protocolos
e, desde a última versão, lançada e m
2017, conversa com todos os sistemas supervisórios da
camada 7, do modelo ISO/OSI, sejam baseados em Windows
ou Unix.
Quanto mais os protocolos forem abertos, padronizados,
robustos, compatíveis, menos tradutores (gateways)
serão necessários, “tornando a comunicação mais rápida,
confiável e disponível, além de independente de fornecedores,
o que, para o owner, é um valor cada vez mais basilar,
preconiza Vieira, ao lembrar que o OPC UA, lançado
em 2008, é um protocolo maduro, e já adotado largamente,
evolução do OPC, criado em 1994, ainda como
“OLE for Process Control”, dependente do DCOM, uma
plataforma base Windows. |
|
|
|
Relacionamento com outros protocolos
“Os dispositivos de campo são conectados ao OPC
UA, através de controladores ou gateways específicos, que
atuam como um conversor entre os protocolos e a estrutura
OPC UA. A vantagem de uma comunicação direta a
um dispositivo de campo, via OPC UA, é que não há necessidade
de nenhuma conversão da informação (semântica)
e/ou do protocolo. Além disso, a maioria dos controladores,
atualmente, fornece apenas acesso limitado às
informações que se originam dos dispositivos conectados
ao controlador, também por causa das limitações de desempenho.
A conectividade direta fornece acesso total às
informações, com um padrão consistente de comunicação
industrial, e um padrão comum de modelagem de informações.
O uso do OPC UA como um padrão comum e
consistente oferece mais flexibilidade de conectividade e,
ao mesmo tempo, acesso seguro” diz Peter Lutz.
A visão da Fundação é fornecer uma solução de comunicação
IIoT consistente e padronizada, para que dispositivos
de diferentes fornecedores sejam capazes de se
comunicar, desde o nível do campo, até o nível do controlador,
e até mesmo na nuvem. Porque OPC UA (IEC
62541) e Ethernet resp., Ethernet APL, e Ethernet TSN
(IEEE 802.3 e 802.1) são padrões internacionais, independentes
do fornecedor, os usuários não terão mais de lidar
com protocolos incompatíveis, ou sistemas proprietários.
A adoção do OPC UA sobre o padrão TSN permitirá que
eles se beneficiem de vários fornecedores, comunicações
ponto-a-ponto, e controle entre sensores, dispositivos de
controle, PLCs e sistemas de controle distribuído, sem a
necessidade de desenvolvimento de software caro e demorado,
ou gateways complicados e pontes.
Reforçando que o OPC-UA é um formato de mensagem
simples, um protocolo chamado de camada de
aplicação, porque se situa na camada de abstração 7, a
mais alta do modelo ISO/OSI, Vieira afirma que, na prática,
isso significa que ele identifica como a informação é
formatada, e pode funcionar sobre qualquer outro protocolo
de nível mais baixo. “A interface entre camadas é
a mesma padronizada pelo então RM-OSI, desde 1983:
feita por PDUs e SDUs, através de pontos de acesso bem
definidos”, resume Vieira, ou seja: “OPC UA roda sobre
qualquer protocolo de camada inferior, como TCP/IP, por
exemplo (camadas 4 e 3), que, por sua vez, pode rodar sobre Ethernet (camadas 2 e
1)”.
Nas palavras de Cassiolato,
isso significa que a
adoção deste padrão aberto
é oportunidade que gera
valor para fornecedores e
usuários, pois, em um universo
em que “a agregação
de informação sobre muitas
camadas é crítica, e de
fundamental importância, o
protocolo de comunicação
fornece a semântica de interoperabilidade
para o mundo
inteligente de sistemas
conectados, oferecendo uma
solução completa para todas
as necessidades de todas as
camadas verticais de acesso
em dispositivos remotos”.
|
|
 |
|
Quando se trata desse
ecossistema com diferentes fornecedores, os especialistas
lembram a variedade de protocolos que transitam com o
OPC UA, e as diversas formas de realizar a conversão e
a tradução, deduzindo pela possibilidade de colocar em
risco a transparência, a convergência e a interoperabilidade.
Nesse sentido – ressalta Santos – “cabe às associações
industriais tecnológicas, prover guidelines e/ou perfis de
integração das suas respectivas tecnologias com o OPC
UA, de forma que essa integração seja padronizada, comum
e independente dos fornecedores. É justamente isso
o que a Associação Profibus & Profinet International (PI)
está fazendo, desde 2015, no que tange
a integração dos protocolos Profinet
e IO Link, com o OPC UA”. |
|

|
Extrapolando para o envio
de informações para a nuvem
(cloud), há possibilidade de uso
do OPC UA pelos instrumentos
e máquinas. No entanto, existem
outras opções. Marcos Giorjiani,
diretor da Beckhoff no Brasil, por
exemplo, lembra do MQTT protocolo consoli- dado,
criado em 1990, que também “pode fazer isso de forma eficiente”. Como o armazenamento local ou em nuvem
independe de protocolos de troca de dados em nível de
aplicação, no entendimento de Vieira, esses “são assuntos
independentes. A maior parte das plantas industriais modernas,
hoje, usa OPC UA, e não trabalha com armazenamento
em nuvem, por exemplo”. |
|
|
|
 |
|
Ao lembrar que OPC UA e MQTT são protocolos desenvolvidos
em épocas diferentes, e com finalidades de
uso diversas, com vantagens peculiares, dependendo dos
cenários de aplicação, Santos entende o assunto como
“uma questão estratégica de cada empresa, seja ela fornecedora
de equipamentos e máquinas ou clientes finais”
e informa que “o desenvolvimento assíncrono do OPC
UA e do MQTT não inviabiliza que eles possam convergir
e possibilitar novos cenários de uso decorrente dessa
convergência. É o que está acontecendo, nesse momento,
com o desenvolvimento do perfil OPC UA Pub/Sub (publish
subscribe), o qual possibilitará o uso do MQTT como
meio de transporte das informações OPC UA, tornando o
OPC UA Pub/Sub mais próximo de cenários de integração
com a nuvem”.
Convivência pacífica
Ressalte-se aí a convivência entre diversos protocolos,
a coexistência de tecnologias diferentes num mesmo
ecossistema, compartilhando cenários de uso comum entre
si, mas com demandas específicas, extraindo de cada
um o que ele tem de melhor em sua especialidade.
A necessidade principal envolve a diferenciação dos
protocolos, para fins de controle e tempo real no chãode-
fábrica, assim como os protocolos desenvolvidos para
fins de integração com o ambiente coorporativo e a nuvem.
Nesse sentido, Santos cita a assinatura de contrato
de cooperação mútua entre a OPC Foundation e Associação
PI, tornando possível a diferenciação dos protocolos
OPC UA, Profinet e IO Link, assim como sua integração
e coexistência.
“A adoção de tecnologias de comunicação maduras e
comprovadas, em conjunto com outras tecnologias, possibilitará
atingir elevados graus de digitalização, em suas
diferentes vertentes”, frisa Marcio Santos.
Esse conceito também é extrapolado para aplicações
baseadas em sinais analógicos, como 4-20mA, que têm
custo inferior de implementação, quando comparado
ao OPC UA. Contudo, a progressiva redução de custos
dos processadores com portas Padrão Ethernet, e múltiplos
protocolos de comunicação embarcadas, tendem a
facilitar a implementação de comunicações digitais em
equipamentos de campo (Camada 1, física, do modelo
ISSO/OSI), que outrora baseavam-se em sinais 4-20mA.
O fundamental, nesse cenário, na visão de Giorjiani,
é que um protocolo Field Bus precisa ser “extremamente
rápido, para poder amostrar as variáveis controladas em
tempo real, e o OPC UA não tem essa característica”. A
utilização do padrão EtherCAT é recomendada pelo diretor
da Beckhoff, pois, “garante uma configuração com
um protocolo de controle extremamente rápido, flexível e
eficiente para dispositivos de campo, inclusive dispositivos
com padrão 4-20mA. E a troca de dados entre controladores,
e entre controladores e o nível corporativo, pode ser
feita via OPC UA”.
Pontos de atenção
Pedro Vieira alerta para a necessidade de o protocolo
de comunicação – qualquer que seja ele – ser mantido
em seu devido lugar, que é o de bastidor, não de protagonista,
uma vez que “acabou a época em que duas soluções
tecnológicas se diferenciavam pelos seus protocolos.
|
|
 |
|
Hoje, precisam se diferenciar por sua funcionalidade, seu
serviço, sua capacidade de habilitar outras tecnologias,
como a Ciência de Dados. A regra comum, se é que há
alguma entre esses conceitos, é a de padrões abertos, interoperáveis,
confiáveis e compatíveis”.
A segurança nas redes industriais é tema lembrado
por Cassiolato: “Qualquer tipo de sabotagem, em operações
automatizadas, gera transtornos e prejuízos incalculáveis.
A análise de riscos, estratégias de prevenção contra
softwares invasores, armas cibernéticas, a gestão de continuidade
de negócios, no caso de incidentes no ambiente
de redes industriais, assim como a implementação de um
ambiente de monitoramento contínuo em uma rede de
automação, são obrigatórias para manter um sistema seguro,
confiável e disponível”.
A migração para o ambiente Industrial de tecnologias
de automação consolidadas, simples, eficientes, e com
ótima relação custo-benefício vem sendo constatada, tais
como IoT, Big Data, etc. “Assim, normas e regras estão cada
vez menos complicadas”, constata Giorjiani, como ponto
positivo, “pois, do contrário, não servirão para atender uma
necessidade de implementação rápida e segura”.
Outro tópico a ser levado em consideração relaciona-
se à necessidade de as tecnologias em si serem facilitadores,
dentro de um projeto de digitalização, proporcionando
redução de custos operacionais, flexibilização
e aumento da produção. Com isso em mente, é de se
esperar que, não apenas uma única tecnologia seja capaz
de prover todos esses ganhos, mas, na realidade, um
conjunto de tecnologias operando de forma convergente,
isso é, ao mesmo tempo e de forma complementar, uma
às outras, num ecossistema digital.
Peter Lutz ressalta que a intenção da OPC Foundation
e da iniciativa FLC não é desenvolver “mais um protocolo”.
A abordagem é estender o OPC UA com recursos
necessários para comunicações em nível de campo,
e combinar esta solução com tecnologias como Single-
Pair Ethernet (SPE) e Advanced Physical Layer (APL), para
cobrir os vários requisitos em aplicações de Automação
de Fábrica e Processos. Essa abordagem contribui para
a convergência do cenário heterogêneo de hoje com as
várias soluções de fieldbus e Ethernet em tempo real. “Ao
estender o OPC UA para incluir os requisitos de aplicativos
em FA e PA, o OPC UA se torna uma alternativa atraente
aos barramentos de campo tradicionais, especialmente
porque fornece uma solução de comunicação completa e
abrangente (transporte mais modelagem de informações
mais semântica comum), do sensor à nuvem, e vice versa.
E inclui recursos como determinismo, segurança funcional,
etc., que permitirão substituir os barramentos de campo
atuais nos médio e longo prazos”.
Um ponto que pode criar um pouco de conflito é se
o OPC UA vai ser um substituto das redes de campo. Em
alguns momentos, isso fica um pouco em evidência – e o
Peter Lutz vai mais nessa linha – e, em outros momentos,
é sutil. “Eu acho que é muito cedo colocar isso como uma
possibilidade técnica real, pois, algumas tecnologias precisariam
se estabelecer primeiro, antes disso acontecer (estou
falando do Ethernet APL e do Ethernet TSN). Somente após
isso acontecer, é que existirá um caminho técnico que permitirá
o OPC UA jogar o jogo pesado no chão-de-fábrica
(real time, determinismo, funções de controle e por aí vai).
O OPC UA descer para o nível de controle, e estar apto a
desempenhar o papel dos FieldBuses atuais, é um cenário
possível, mas isso ainda demandará um tempo relativamente
grande, tanto no aspecto técnico, quanto no estratégico.
Particularmente, acredito que devemos fomentar o OPC UA
no que ele pode contribuir de melhor para a digitalização,
que é a integração e a convergência horizontal/vertical entre
sistemas. Pensar em OPC UA real time é algo tão longe da
minha realidade, que não consigo enxergar se, quando e
como isso vai acontecer”, comenta Marcio Santos.
O diretor da OPC lembra, ainda, que a digitalização
e os novos serviços digitais exigem a integração de tecnologias
de TI com produtos, sistemas, soluções e serviços
OT em suas cadeias de valor completas, que vão, desde o
design e produção, até a manutenção. Protocolos são soluções
para o campo e, portanto, são usados para conectar
dispositivos de campo aos controladores (Controle Lógico
Programável, Controle de Movimento rol) ou sistemas de
controle distribuído (DCS). É por isso que, em um mundo
digital integrado, uma conectividade direta e padronizada
entre dispositivos e aplicativos do campo à nuvem, e viceversa,
é essencial. Para trocar informações relacionadas à
produção e ao processo, dentro e fora de uma fábrica,
com uma única solução de comunicação IIoT. E o OPC
UA está fornecendo uma estrutura industrial (como uma
coleção de “blocos de solução”), que pode ser usada de
forma flexível, e aplicada a diversas áreas em TI e TO, em
Automação de Fábrica e de Processos.
Os mecanismos de modelagem e troca de informações
seguem regras e práticas comuns (por exemplo, segurança,
serviços de comunicação, qualidade de serviço).
No entanto, para suportar a ampla gama de requisitos em
TI e TO, são necessários recursos e conjuntos de recursos
específicos, por exemplo, segurança funcional para comunicações,
em nível de campo, ou big data, para conectividade
em nuvem. A vantagem da estrutura industrial OPC
UA é que os conceitos podem ser facilmente reutilizados,
e as adaptações a novos requisitos ou novas tendências
e tecnologias são facilmente possíveis. Isso fornece um
alto nível de padronização, em combinação com um alto
nível de flexibilidade.
“O 5G está facilitando a conectividade sem fio, em
combinação com alta largura de banda e baixa latência e,
portanto, é altamente interessante e atraente, como tecnologia
de comunicação industrial, para o chão-de-fábrica.
Como a padronização do 5G é um processo aberto e
direcionado a contribuições entre empresas de telecomunicações
de todo o mundo, garantindo, um padrão aberto,
interoperável e internacional pode ser esperado”, finaliza
Peter Lutz. |
|
Conversando sobre Ethernet |
A Controle & Instrumentação perguntou a mestre Marcos Peluso, distinguished technologist que acabou de se aposentar, qual o impacto do Ethernet nos outros protocolos... Ele respondeu... senta, que lá vem história! |

|
“A transformação digital atingiu praticamente todos
os ramos da atividade humana, trazendo enormes
benefícios. A tecnologia disponível hoje é poderosíssima,
e permite um aumento considerável no rendimento
e segurança das plantas industriais, e na segurança
e saúde das pessoas e meio ambiente. Enquanto, em
nossas vidas pessoais e em alguns setores da indústria,
é relativamente fácil acompanhar as revoluções e
evoluções tecnológicas, na indústria de processo, fica
muito difícil mudar tudo, da noite para o dia. Mas,
a transição pode ser feita com muito sucesso, se planejada
e implementada bem. Temos de lembrar que,
por muito tempo, ainda teremos de conviver com a
base instalada e, para isto, teremos de estar preparados
para que esta base possa trazer todos os benefícios
de que a transformação digital potencializa. Por isso,
é importante compreender um pouco da história por
trás do que está disponível hoje, para facilitar
sua integração e evitar percalços do passado.
Aqui vai um pouquinho de história. Se
governantes estudassem história, a vida
seria melhor... |
|
|
A instrumentação digital começou
a ser utilizada há quase 40 anos. Inicialmente,
só o processamento de sinais no
interior dos instrumentos de campo era
digital, enquanto a comunicação com sistemas
de controle continuava analógica (0-20 mA,
4-20 mA, 10-50 mA, etc). Isto porque os sistemas de
controle ainda eram analógicos. Com o surgimento
de sistemas de controle digitais, alguns fornecedores
acordaram para o fato de que não fazia sentido converter
o sinal digital do instrumento para analógico, e
depois reconvertê-lo, de analógico para digital, no sistema.
E que o sinal digital poderia oferecer muito mais
do que somente informar o valor da variável primária.
Ele poderia, por exemplo, conter dados sobre a saúde
da variável e do instrumento, fornecer informações
sobre variáveis auxiliares, dados estatísticos sobre as
variáveis de processo, etc. E, com isso, surgiram vários
protocolos de comunicação proprietários, que permitiam
comunicação puramente digital, entre o sistema
digital de controle e os instrumentos digitais de campo.
Em alguns casos, a comunicação era de ponto a
ponto e, em outros, os instrumentos eram ligados em
barramento, o que permitia a redução na quantidade
de cabos.
Ainda que tecnicamente interessante, estas soluções
apresentavam um problema sério, pois, para
auferir os benefícios da tecnologia, o usuário era
obrigado a adquirir sistema e instrumentos de campo
do mesmo fornecedor. Era um casamento sem
divórcio.
Como os sinais analógicos em 4-20mA e 0-20 mA
ainda eram, e continuam sendo, amplamente utilizados
na indústria, surgiu a ideia de desenvolver uma
comunicação híbrida, onde o sinal digital compartilhava
o mesmo par de fios com o sinal analógico. Desta
forma, a variável primária do instrumento poderia ser
enviada pelo sinal analógico convencional, porém,
também poderia ser enviada de forma digital. Com a
vantagem adicional de que outras variáveis do instrumento,
seus parâmetros de configuração, diagnósticos
e alertas poderiam também ser acessados digitalmente.
Este é o protocolo HART, que é amplamente
utilizado na indústria. Mas, devo dizer que,
na maior parte das aplicações, as variáveis
e dados digitais são drasticamente subutilizados.
Vou explicar o porquê disso, mais
adiante.
Interessados nas vantagens que a estandardização
de uma comunicação puramente
digital e em rede poderia trazer para
o mercado, usuários e fornecedores (“motivados”
pelos primeiros) participaram no desenvolvimento
de um conjunto de normas com esta finalidade.
A indústria de petróleo foi uma grande incentivadora,
pois, estava e está muito interessada em reduzir, ou
mesmo eliminar, o número de cabos e respectiva infraestrutura
nas plataformas. Mas, outra grande motivação
vem do fato que a instrumentação digital oferece
uma visão muito mais detalhada sobre a operação e
saúde das plantas, permitindo monitoração, controle,
e mesmo manutenção remotas, viabilizando a redução
de pessoal presente nas plantas. Isso é particularmente
importante nas plataformas de óleo e gás.
Bem, a norma e os produtos vieram, mas, como
não poderia deixar de ser, infelizmente, não houve
consenso, e acabamos com várias normas (Fieldbus,
Profibus, DeviceNet, etc), criando um bocado de
confusão na cabeça dos usuários. E também criaram
problemas para os próprios fabricantes, que tiveram
de desenvolver e suportar produtos com os diversos
protocolos.
Apesar da existência dos diversos protocolos de comunicação
digital, e a despeito da orientação dada pela
direção das grandes empresas usuárias, para que eles
fossem utilizados, uma boa parte da indústria continuou
a utilizar comunicação analógica. E muitos dos que usaram
comunicação digital a instalaram, comissionaram e
a utilizaram como no passado, desperdiçando tempo e
dinheiro, e a oportunidade de uma operação e manutenção
mais eficiente. E boa parte dos sistemas de segurança
somente podem utilizar o sinal analógico. Alguns
permitem um acesso “policiado” e restrito, via HART.
Como praticamente todos os instrumentos de campo
analógicos suportam HART, muita gente diz que usa
HART, mas na realidade só o sinal analógico é utilizado.
HART acaba sendo usado somente para eventuais mudanças
de configuração, ou manutenção reativa. Muitos
não se deram ao trabalho de incorporar a informação
digital às estratégias de controle, segurança e manutenção
da planta. Outros desistiram da tarefa, quando se
assustaram com o número de alarmes recebidos por falta
de uma configuração adequada. E outros ainda desanimaram,
diante do desafio imposto pela falta de consistência
na terminologia utilizada pela indústria. Uma
mesma função acaba recebendo nomes diferentes, por
fornecedores diferentes, e até mesmo por um mesmo
fornecedor. Parte da razão por trás disto é que as normas
foram escritas no tempo em que a tecnologia limitava
o número de caracteres, obrigando o uso de acrônimos
e abreviações, o que dificultava a interpretação. E,
pior ainda, quando apresentados para pessoas que não
são familiarizadas com a língua inglesa. E a lentidão na
comunicação, quando comparada com o que estamos
acostumados hoje, era tolerada.
Com o avanço da eletrônica, a capacidade de
processamento e armazenamento dos instrumentos e
sistemas aumentou, e alguns fornecedores tomaram a
liberdade de batizar parâmetros com nomes mais compreensíveis,
o que seria bom, não fosse o fato de que
não havia consistência entre diferentes fornecedores, e
até mesmo entre revisões diferentes de produtos de um
mesmo fornecedor.
Isso pode não ser um grande problema quando se
trabalha diretamente com um instrumento, mas é um
pesadelo para a automatização e consistência de comissionamento,
operação, manutenção e gerenciamento
de ativos. Felizmente, organizações como o FieldComm
Group, Probibus Organization, OPC UA e OVDA resolveram
reformar a terminologia, e realmente policiar consistência.
E, para estender os benefícios à base instalada,
criar um software que permitirá a “tradução” dos nomes
incompreensíveis para os nomes inteligíveis, e realmente
normatizados. Isso será de fundamental importância
para permitir que a base instalada seja parte ativa, nesta
quarta revolução industrial.
Mas, é claro que novos projetos terão à disposição
tecnologias de última geração. Como quase tudo que
nos cerca hoje é muito prático, fácil, confiável e rápido,
há uma expectativa de que os instrumentos de campo
possam se comportar da mesma forma. Minha neta de
cinco anos queria ampliar a imagem da televisão com os
dedos. É esperada a velocidade e capacidade de transmissão
de dados proporcionado pela comunicação via
Ethernet através de fios, fibra ótica ou por rádio. E que
os instrumentos sejam realmente “Plug-and-Play”, e não
“Plug-and-Pray”.
A indústria, no passado, até que tentou fazer isso.
Uma empresa chegou a desenvolver um transmissor
com fibra ótica. O sinal e a alimentação eram transmitidos
por fibra, era como se o instrumento tivesse um
pequeno painel solar dentro dele, que convertia a energia
da luz em energia elétrica, para alimentar o circuito
eletrônico. Funcionava bem, mas tinha um problema,
que fez com que a ideia fosse arquivada: se a fibra rompesse,
ou fosse desligada sem o devido cuidado, a energia
da luz era tal que podia causar uma explosão em
áreas classificadas. Um dos primeiros instrumentos em
Fieldbus era um transmissor multivariável com fibra ótica,
mas alimentado por fios. Depois disso, chegou a ser
feito um transmissor com Ethernet. Ele precisava de um
cabo para alimentação, e outro para o sinal, transmitido
através da Ethernet. O transmissor era bom no inverno,
pois, servia de aquecedor. A tecnologia disponível
naquela época dificultava a implementação de transmissores
para área classificada, devido ao consumo de
energia. E não era justificável economicamente, pois, o
ganho em velocidade não justificava o custo dos cabos
e instalação. Outro projeto engavetado. E como a indústria
utilizava – e utiliza até hoje – o 4-20 mA para
controle, e eventualmente o Hart para configuração e
diagnóstico, o ganho em velocidade não era tão atrativo.
Ouvi o mesmo argumento muitas vezes, em relação ao
Fieldbus e Profibus. Mesmo com todas as vantagens do
Fieldbus e Profibus, boa parte da indústria preferiu ficar
com o 4-20 mA, porque as novas tecnologias iriam mudar
suas práticas de instalação, integração com o sistema
de controle, etc.
Isso explica um pouco porque as coisas são como
são. Os instrumentos de campo hoje oferecem muito
mais do que ofereciam há bem pouco tempo, mas
bem poucos oferecem comunicação via Ethernet. Estes,
normalmente, requerem cabos para alimentação
e para sinal.
Mas o uso de Ethernet, para acessar os instrumentos
de campo, aumentou muito. Os instrumentos de campo
em HART, Fieldbus, Profibus, ControlNet, e até analógico
ou discreto, podem ser ligados a gateways no campo,
e de lá aos sistemas de controle, via Ethernet redundante,
através de fios, fibra ótica ou Wi-Fi.
Os segmentos em Fieldbus ou Profibus podem ser
conectados a um linking device ou um acoplador, que
transfere os sinais provenientes de dois ou mais segmentos
de campo para um barramento de maior velocidade, e este barramento é então conectado ao sistema de
controle, gerenciamento de dados, etc. O Fieldbus faz
isso através do HSE (High Speed Ethernet) onde, como o
nome diz, as camadas superiores do protocolo de comunicação
são Fieldbus, e as camadas inferiores, Ethernet.
Profibus faz isso através de Profibus DP de maior velocidade
ou Profinet, que é totalmente compatível com
Profibus DP, nas camadas superiores, e usa Ethernet nas
inferiores. Da mesma forma existe o Hart IP, que consiste
em enviar múltiplas mensagens Hart, através de uma
mensagem Ethernet. Pode-se usar um mutliplexer, para
capturar as mensagens Hart de múltiplos instrumentos,
e enviá-las para o sistema de controle e/ou de gerenciamento
de ativos.
Outros protocolos, como DeviceNet e ControlNet,
usam CIP (Common Industrial Protocol), e a diferença
básica entre as duas é o meio físico. E basicamente o
mesmo protocolo é usado, tendo Ethernet como meio
físico – no que recebeu o nome de Ethernet IP. Ou seja,
a indústria já vem usando, há bastante tempo, a Ethernet,
para transmitir informação proveniente de redes
com menor taxa de transferência de dados, ou mesmo
informação proveniente de múltiplos instrumentos analógicos
ou discretos. Na manufatura, ou mesmo nos parques
da Disney, você pode ver umas caixinhas rebecendo
dados de medidores, chaves de nível, detectores de
movimento, chaves limite, etc., e enviando tudo isso, via
uma rede de alta velocidade, para o sistema de controle
e segurança das atrações.
Mas, então, por que não ligavam os instrumentos
diretamente numa rede de alta velocidade ou, melhor
ainda, a uma rede Ethernet, como fazemos em casa ou
no escritório?
Existiam várias limitações. A principal delas vinha
do fato de que você teria de substituir os dois fios, que a
maioria dos instrumentos usam, por quatro ou mais fios.
A instalação acabava custando mais, e requeria cuidados
especiais para instalação em áreas industriais, onde
o ambiente é muito agressivo. O segundo ponto era o
comprimento do cabo. Quanto maior a frequência de
comunicação, mais curto deve ser o cabo. A Ethernet
que usamos em casa ou no escritório, de 10 Mbps ou
100 Mbps (Megabits per second), o cabo mais comumente
usado não deve ultrapassar 100 m. Este limite
na indústria de processo é problemático. Na indústria
de manufatura, isto não chega a ser um problema, pois,
as distâncias entre componentes são bem mais curtas.
É claro que se podem utilizar repetidores, ou usar um
acoplador, que transfere os dados para fibra ótica, que
pode atingir distâncias muito longas. E o raio mínimo
permitido para a curvatura do cabo é bem maior do que
os cabos usados para HART ou fieldbuses. Tudo isso tornaria
o projeto e a instalação mais complexa.
A outra limitação é que, na indústria de processo,
muitos instrumentos são instalados em áreas classificadas,
onde é preciso limitar o uso de energia, e também
a sua capacidade de armazenar essa energia. Com o
aumento da taxa de comunicação e demanda de processamento,
o consumo de energia sobe, e o projeto e
aprovação dos instrumentos com segurança intrínseca se
tornava mais complicado.
Muito bem, um consórcio, formado pelo FieldComm
Group, Profibus-Profinet, ODVA (DeviceNet, Control-
Net, Ethernet IP) e outras entidades, está em fase final
de desenvolvimento e testes de normas, para o uso de
Ethernet em instrumentos de campo. |
 |
|
Vale lembrar que estas instituições são formadas
por fornecedores e usuários, com larga experiencia na
indústria de controle de processo. O dia-a-dia deles é
trabalhar com a base instalada, e buscar soluções para a
indústria do futuro. E que esta indústria utiliza dezenas
ou centenas de milhares de instrumentos de diversos tipos
e espalhados em grandes áreas.
Esta tecnologia é chamada de Advanced Physical
Layer – APL. A ideia básica é permitir, como acontece
com Hart, Fieldbus, e Profibus PA, que a comunicação e
alimentação elétrica dos instrumentos seja feita por dois
fios, e usando um protocolo à base de Ethernet. Como,
em Ethernet, o endereçamento de cada mensagem usa
uma quantidade enorme de bytes, se comparado com
o tamanho de uma mensagem típica usada pelos instrumentos
atuais, foi necessário fazer uns ajustes, aqui
e ali. Os chips comerciais para Ethernet também não
poderiam ser usados, pois, eles não seriam compatíveis
com instrumentos intrinsicamente seguros.
Para contornar estes problemas, foram desenvolvidos
chips específicos para este tipo de aplicação industrial,
mas que também poderiam ser usados em outras
aplicações industriais. Os testes indicam que a solução
é robusta, e atende aos requisitos. Como indicado na
figura abaixo, os instrumentos no campo podem ser
ligados a um comutador (switch) Ethernet especializado,
que fornece energia intrinsicamente segura para os
instrumentos, e recebe e comuta as mensagens para a
rede Ethernet da planta. O comutador pode receber 4,
8 ou mais instrumentos, dependendo do que o mercado
terá para oferecer. O comprimento do cabo, entre
o comutador e o instrumento, pode chegar a 1.000
metros. Os comutadores (switches) Ethernet são ligados
à rede Ethernet de campo. Esta rede é ligada a um
comutador, que recebe sinal e fornece energia para a
rede de campo. Dali, a informação é roteada através
de firewalls para os consumidores da planta, tais como
sistema de controle, gerenciamento de ativos, etc. e,
através de mais firewalls e diodo de dados, para rede
corporativa e consumidores externos. Dados coletados
pelos roteadores podem também ser transmitidos via
Wi-Fi. Com 5G, se os políticos deixarem, a velocidade
de comunicação sem fio pode ser muito maior, com
quase nenhuma latência.
A tecnologia Advanced Physical Layer – APL foi
testada com sucesso, na Basf, em 2019, numa rede
com protótipos de vários fornecedores, e apresentada
na Reunião Geral NAMUR, de novembro de 2019,
e no ARC Advisory Group Forum, em fevereiro de
2020, quando a ABB mostrou uma implementação
que efetivamente eliminou todos os gateways e conversões
de protocolo, de um medidor de nível para a
rede corporativa. A Ethernet-APL promete simplificar
a arquitetura, e aumentar a largura de banda para comunicação
de instrumentos digitais, algo como deixar
a frequência 300 vezes mais rápida do que a dos protocolos
atuais.
A Ethernet-APL é baseada no padrão 802.3cg-2019
(10BASE-T1L), aprovado pelo IEEE, que estende o padrão
Ethernet 802.3 para incluir fiação de par único,
em distâncias de até 1.000 metros, com o fornecimento
opcional de energia para dispositivos, e é de particular
importância para as indústrias de processo, já que
estende o 10BASE-T1L para uso em áreas classificadas
– o comitê técnico IEC PT 60079-47 está trabalhando na
chamada Ethernet Intrinsecamente Segura de Dois Fios
(2-WISE), para cumprir os requisitos para dispositivos até
Zona 0, 1 e 2 / Divisão 1 e 2. A especificação final (IEC
TS 60079-47) é esperada para o ano que vem.
Tudo indica que o desenvolvimento do novo nível
físico, para comunicação com os instrumentos, está
indo muito bem, deve dar conta do recado, e será de
grande benefício para a indústria – se for bem implementado.
Pois, o desafio da boa instalação e manutenção
continua, mais presente do que nunca. Parece
que as regras básicas da Física foram esquecidas, e o
pessoal de instalação não tem recebido o treinamento
adequado. Nas minhas andanças pelo mundo, vi muita
instalação mal feita, com todo tipo de comunicação;
de 4-20 mA, a fieldbuses e Wireless. Este último não
requer cabos, mesmo assim, o pessoal consegue fazer
coisas inacreditáveis. Isto acontece igualmente em
países ricos ou pobres. Treinamento adequado é fundamental,
para qualquer que seja a tecnologia sendo
utilizada.
Uma rede Ethernet, ainda que em menor velocidade
(este projeto é para 10 Mbps), é mais sensível a
enganos na instalação. E a manutenção não é a que a
indústria de hoje está acostumada. Vai requerer treinamento,
mas a moçada que está entrando no mercado
de trabalho foi criada com celulares, computadores e
vídeo games; eles ou elas não terão problemas para
aprender.
Outro grande desafio é a estandardização na transferência
dos dados. A ideia é utilizar OPC UA que está
organizando, entre outras, a semântica, e aquela tradução
automática e convergência dos diversos termos, presentes
na indústria, para os termos padronizados. E FDI
para uma apresentação dos dados também, de forma
padronizada. É de fundamental importância, que parâmetros
de uso comuns, tais como, por exemplo, Unidade
de Engenharia, possam ser entendidos e apresentados
da mesma forma em instrumentos de fabricantes
diferentes, em diferentes sistemas. Como dito anteriormente,
isso eliminaria a confusão que existe hoje, e facilitaria
muito a organização e manipulação de dados, na
planta ou na nuvem.
Se tudo isso for feito direitinho, a integração de
dados, que é tão importante para a Indústria 4.0, será
muito fácil, rápida e segura. |
|
|
|
|
|
|
|
|
|
|
|
LEIA MAIS
NA EDIÇÃO IMPRESSA |
|
DESEJANDO
MAIS INFORMAÇÕES: redacao@editoravalete.com.br
|
|
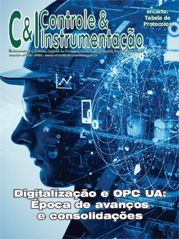 |
Clique na capa da revista para
ler a edição na íntegra |
|
|