Revista Controle & Instrumentação Edição nº 223 2016
|
|
¤
Cover Page
|
Protocolos na Indústria 4.0 |
|
|
 |
|
Todos buscamos otimizar os processos para oferecer
os melhores produtos. E trabalhamos com velocidades
cada vez maiores, buscamos reduzir as paradas, ter produção sem falhas e estruturas interconectadas horizontal e
verticalmente, comunicação homem-máquina e máquinamáquina. Isso tudo se já não existe nas plantas, existe ao
menos nos planos das empresas.
Porque está acontecendo gradualmente uma mudança
que vai alterar permanentemente os processos de produção,
com tecnologias já dominadas. O resultado da interação dessas tecnologias está sendo denominado de IoT ou Indústria
4.0 ou ainda outros nomes. Não é uma revolução, é
um melhor uso de oportunidades tornadas possíveis
pela interação de tecnologias disponíveis hoje. E
esse novo conceito vai continuar a evoluir à medida que evoluírem essas mesmas tecnologias. Jonas
Berge, diretor de tecnologias aplicadas da Emerson
Automation Solutions, em Singapura, ressalta que Indústria 4.0 não é o mesmo que IIoT (Internet Industrial
das Coisas). “O conceito de Indústria 4.0 é muito mais amplo
do que o de IIoT – que desempenha um papel na indústria”.
Desde que foi discutida pela primeira vez na Hannover
Fair de 2011, a Indústria 4.0 se tornou algo que todas as
empresas – usuários finais e fornecedores -, têm buscado.
Não se trata apenas de máquinas que se comunicam entre
si – isso já acontece há anos – nem é sobre uma geladeira
ser capaz de comprar o que falta, nem sobre fábricas que
funcionam sozinhas. Tudo isso tem sido discutido desde os
anos 1980. A Indústria 4.0 é uma combinação de sistemas
computacionais controlando sistemas físicos onde os produtos, processos e serviços se comunicam entre si e com as
pessoas em uma rede global. O que a Indústria 4.0 tem de
diferente são as tecnologias baseadas na Internet que fornecem conectividade para tudo se comunicar – conceito que
também não é novo mas parou ao longo do caminho
várias vezes por conta da divisão de interesses.
À medida que a Indústria 4.0 se torna realidade, será possível se conectar a qualquer dispositivo que tenha uma porta Ethernet, independentemente do que seja e de onde esteja. Mas
nada disso acontecerá sem uma rede capaz de
transportar as informações entre todos os lugares, em
tempo real, com desempenho que exigirá tecnologias com
mais capacidade do que temos hoje. E é nesse ponto que
as dúvidas surgem, se não na infraestrutura externa, muito
na infraestrutura de redes dentro das empresas. |
|
 |
“Com as informações que os protocolos atuais disponibilizam dos equipamentos já é possível desenvolver alguns projetos que nos levam a Indústria 4.0”. |
|
|
“É importante lembrar que há 20 anos, empresas
como a Emerson propunham o amplo uso de instrumentos inteligentes, a interligação de todos elementos
da estrutura de controle através de protocolos de
comunicação abertos, comunicação entre os
instrumentos de campo, o uso de programas de análises de dados para melhoria de
produtividade, qualidade e manutenção
de plantas industriais. Mas a conectividade
era, na maioria das vezes, restrita à planta
ou à empresa, formando uma Intranet das
Coisas. Na época, a internet ainda engatinhava (alguém ainda se lembra do ruído do modem
tentando conectar com a internet através de uma linha
telefônica?) e se alguém falasse de computação ou armazenamento de dados na nuvem, as pessoas olhariam
para o céu. Como o conceito era novo e requeria mudanças na maneira tradicional de fazer as coisas, vários
usuários, a despeito de terem adquirido equipamentos de
última geração, só foram se beneficiar da nova tecnologia bem mais tarde. A adaptação às novas práticas e a
exploração do que já estava à disposição deles demandou tempo e resolução. E até mesmo os fornecedores demoraram a aceitar a transição. Muitos deles não sabiam
explorar o potencial de seus próprios equipamentos.
Desde então, houve uma tremenda evolução da tecnologia digital, ampliando e abrindo novos horizontes em
todos ramos da atividade humana. E as novas gerações
nasceram e cresceram com ela. E os instrumentos inteligentes se tornaram mais poderosos, oferecendo um valioso leque de funções e diagnósticos. As redes de comunicação permitiram fácil e rápido acesso aos dados . Os
sistemas de controle e gerenciamento de ativos passaram
a oferecer aplicativos poderosos para operação, otimiza-
ção e manutenção das plantas industriais. O desenvolvimento da tecnologia wireless permitiu a instalação fácil e
econômica de novos pontos de medição e controle que
ampliaram a visão e conhecimento do processo, do estado dos ativos da planta e das condições de seguran-
ça do processo, equipamento e pessoal. Eles ajudam a
monitorar e controlar importantes aspectos do processo
que até então eram desconhecidos ou ignorados. Alguns
destes instrumentos wireless são não-intrusivos, pois não
requerem tomadas, inserções ou paradas do processo
para serem instalados. É possível instala-los e coloca-los
em operação em questão de minutos. Eles têm permitido,
por exemplo, detectar custosos vazamentos de válvulas
que até então nunca tinham sido antes notados. Mas uma
das maiores vantagens oferecidas pela conectividade é a
facilidade com que aplicativos possam ser gerados e instalados usando os dados que sempre estiveram disponíveis
na planta. Estes aplicativos podem transformar os dados
em informações e recomendações valiosas para o pessoal
de operação, manutenção e gerencia da planta. E, como
acontece com os celulares inteligentes, eles podem ser
gerados por especialistas de diversas áreas e diferentes
empresas. Eles podem ser para otimizar controle de
turbinas, para diagnosticar desempenho de diversos tipos de equipamento, etc. Estes aplicativos podem funcionar com os mais diversos
tipos de sistemas de controle, monitoração
de ativos, PLCs, Scada, históricos, etc”, lembra Mestre Marcos Peluso, distinguished technologist da Emerson.
Ainda hoje, um grande número de plantas
utilizam somente o 4-20 mA dos instrumentos inteligentes, a despeito que estes instrumentos disponham de
protocolo Hart para configuração e acesso a diagnósticos.
E cada instrumento conectado através de um ou dois pares
de fios. Há uns 20 anos, os protocolos de comunicação puramente digitais passaram a ser utilizadas em muitas novas
instalações. Com eles, um par de fios pode suportar vários
instrumentos e o acesso a dados de diagnóstico e múltiplas
variáveis ficou muito mais fácil e rápido.
Ainda que um dia teremos protocolos semelhantes a
ethernet com capacidade de transferir dados mais rápido
e mais eficiente e também usar dois fios para dados e
alimentação, e ser intrinsicamente seguro, permitir longa
distância etc, ainda estamos muito longe disso. Tem muita
gente de peso trabalhando em uma norma aberta para
isso, mas até aqui nada de concreto. Existem soluções
proprietárias, que podem parecer promissoras, mas tem
muito chão para demonstrar na prática que funcionam e
que são economicamente viáveis.
“Não vejo problema no uso de ethernet em um nível
superior, onde coleções de dados de gateways, multiplexers, bancos de IO etc possam ser acessados via Ethernet.
Nestes casos, as limitações que os instrumentos de campo
têm não se aplicam totalmente”, ressalta Mestre Peluso.
A ideia de fazer cada instrumento ter seu próprio
web page ou profile publicado remete ao fato de que
as condições ambientais da maioria da plantas industriais
não são propícias para a Ethernet como a conhecemos
hoje. Existem muitas limitações em relação a seguranca
intrínsica para áreas classificadas, distâncias suportadas
por Ethernet com fio, custo e confiabilidade de chaves
(switches) e roteadores instalados no campo, se devemos
trocar dois fios por quatro ou mais fios, robustez, interferência eletromagnética etc. Para a maioria dos instrumentos de campo, a taxa de transmissão dos protocolos
existentes é mais do que satisfatória. E é bom lembrar que
nem os instrumentos têm taxa de atualização muito rápida, nem as malhas de controle, com algumas exceções,
requerem maiores velocidades. Pelo contrário, alguns até
limitam a velocidade para evitar desgaste de equipamento. A velocidade é importante para a transferência de um grande número de dados, como é o caso de alguns instrumentos complexos. As mensagens publicadas repetidamente pela maioria dos instrumentos de campo têm
menos de 10 bytes. Um mensagem em Ethernet, como
usada hoje, tem um overhead de 64 bytes ou mais. No
frigir dos ovos, a velocidade real da rede não é tão grande
quanto se imagina.
Agora, com a IIoT, os protocolos estão mostrando
alguns limites. Porque no mundo dos protocolos, trabalham-se taxas de dados na faixa de 1 a 20 Mbit e tempos
de resposta de 20 ms. Mas, a comunicação em tempo
real precisa de tempos de resposta menores que 100 µseg
e taxas de dados maiores que 100 Mbit. Por conta disso é que se fala da necessidade em usar os protocolos
de Ethernet Industrial – Profinet, Ethernet / IP, EtherCAT,
Powerlink ou Sercos, este último já estabelecido há muito tempo em TI. Como aconteceu na guerra dos buses
dos anos 80, nenhum padrão deve emergir como único
e várias soluções estão sendo utilizadas. Veja que sempre
que uma velocidade mais rápida é necessária, a Ethernet
Industrial leva vantagem no desempenho. Mas os protocolos existentes ainda têm espaço para crescer, ainda que
a Ethernet Industrial tenha começado a ocupar alguns
espaços tradicionais do Fieldbus. Ethernet industrial tem
sido usada na indústria de manufatura, onde ambiente,
instalação, etc. são diferentes.
Alguns dizem que a IIoT usará os padrões de TI (Tecnologia da Informação); outros, que os padrões serão os
de TO/TA (Tecnologia de Operação/Tecnologia de Automação). E ambos os grupos estão corretos já que existem
diferentes níveis na arquitetura IIoT, com as muitas tecnologias existentes. Porque a IIoT abrange de instrumenta-
ção e controle a TI, e não dá para uma pessoa compreender tudo. E, mesmo com a arquitetura correta, é preciso
atenção para não ficar preso num único fornecedor e,
ainda, garantir que a arquitetura possa evoluir com os padrões e tecnologias para que se aproveitem as novidades
tecnológicas vindouras. Muitos tiveram problemas com
tecnologias proprietárias e desejam evitar isso no cenário
de IIoT que se desenha, mas qual modelo usar quando o
assunto é conectividade e redes?
Quando pensamos em Indústria 4.0 – onde temos o
universo cibernético, a conexão de pessoas, informações
e máquinas – promovendo a evolução dos sistemas de inteligência da automação, mudando a operação e manutenção nas plantas como conhecemos, somos remetidos
a pensar quais as tecnologias já nos permitem enxergar
estas soluções aplicadas. E, como todos os protocolos
permitem a conexão de informações, talvez seja necessário utilizar gateways ou servidores de OPC para conectar todas as informações, todavia, quando pensamos em
informações horizontais e verticais, sem a necessidade
de conversores (ou pelo menos com o mínimo possível),
redes que trabalham em padrões Ethernet têm vantagens
sobre as demais, pois, a partir de um padrão utilizado
em toda a indústria, tanto a TI quanto a TO e, porque
não, a TE – automação de sistemas elétricos – convergem
e, a partir de um único ponto nessa conexão, podemos
disponibilizar informações para todos os níveis, levando
até a Nuvem para processamento (Big Data) e tomada de
decisões, utilizando-se de mineração de dados e aprendizado de máquina.
Nesse cenário, protocolos como Profinet e Ethernet/IP, por exemplo, facilitam a inserção na Indústria 4.0,
lembrando que questões como cibersegurança e integração com o IIoT passam a fazer parte da agenda dos engenheiros de automação, que estão pavimentando a 4a
(R)evolução Industrial.
Jonas Berge lembra que o conceito de Indústria 4.0
é muito mais amplo. “ Prefiro falar IIoT. A rede digital
desempenha um papel na parte IIoT da Indústria 4.0, um
papel muito importante na arquitetura da IIoT que precisa de centenas de milhares de sensores numa planta, o
que seria impraticável com sinais 4-20 e on-off apenas.
As tecnologias wireless e fieldbus são uma maneira mais
simples de adicionar todos esses sensores. É por isso que
as redes de sensores digitais são tão importantes – e onde
atuam o Fieldbus e o WirelessHart ou um Profibus – usado para monitorar o equipamento elétrico num CCM”.
Escolher as tecnologias certas para a arquitetura é
fundamental para a viabilidade no longo prazo do sistema
IIoT. E qualquer sistema complexo se torna mais simples
dividido. Então, uma arquitetura em camadas para IIoT
faz sentido porque essa abordagem permite que qualquer camada seja comutada à medida que a tecnologia evolui
sem que se tenha que alterar todas as outras camadas.
Por exemplo, você pode alterar o backhaul do celular
para banda larga, mudar o provedor da nuvem, mudar
o middleware, alterar o firewall para diodo de dados, e
ainda misturar fieldbus com redes de sensores wireless e
assim por diante. E, ao construir a arquitetura com padrões, é possível mudar de monitoramento interno para
terceirizado, e vice-versa. |
|
 |
Os protocolos de rede industrial foram a fronteira que separou a época da automação
convencional, focada na discussão de controle de processo, pura e simplesmente e, promoveu
o salto da informação dentro da automação industrial, permitindo que, além de controle,
pudéssemos obter informações para gerenciamento de manutenção, tanto de dispositivos,
quanto de processos. Com isso, inauguramos a era da gestão na automação e controle de
processos. Como é natural, os protocolos de rede industrial tenderam a tecnologias e soluções
que foram caracterizadas por usuários e desenvolvedores de produtos. Temos protocolos
industriais baseados no padrão elétrico RS-485, o Prof bus, por exemplo, e na evolução,
utilizando o padrão Ethernet, temos o Prof net. |
|
|
Porque as “coisas” na Internet Industrial das Coisas
são equipamentos como compressores, bombas, trocadores de calor, torres de resfriamento, sopradores, trocadores de calor arrefecidos a ar, válvulas de controle, válvulas
on-off inteligentes, válvula de alívio, e uma série de outros
equipamentos. As plantas já possuem milhares de sensores
conectados ao sistema de controle, mas esses são focados
principalmente na monitoração e controle do processo,
portanto, muitos sensores adicionais são necessários para
cobrir o que falta monitorar, o próprio equipamento que
deve receber sensores para permitir que seja monitorado
remotamente e permita a detecção permanente de condições de desempenho, garantindo disponibilidade e eficiência energética. Com centenas ou milhares de “coisas”
a serem monitoradas, essas aplicações se prestam muito
bem à rede digital, wireless ou não.
E porque serão milhares de sensores é crítico selecionar os de tecnologias que durarão sem problemas e sem
manutenção por muitos anos, sensores construídos para
resistir a fluidos corrosivos e
abrasivos, pressões e vácuo
extremamente elevados, altas temperaturas criogênicas,
vibração, EMI, RFI, entrada
de água e poeira, adequados para áreas perigosas, etc.
Bons sensores são críticos
para executar e manter o próprio sistema IIoT.
Mestre Marcos Peluso
enfatiza alguns pontos. “ A Indústria 4.0 tem o objetivo básico de habilitar amplo e fácil
acesso a dados e criar processos analíticos que convertam estes dados em informações
voltadas para o aumento da produtividade, qualidade e
segurança. Isto é alavancado pelo uso de IIoT, a versão industrial da Internet das Coisas, comunicação interoperável entre equipamentos, computação e armazenamento
na nuvem, compartilhamento de dados dentro e fora da
empresa e aplicativos especializados para cada tipo de
função. Mas para que tudo isso ocorra, é fundamental
que haja segurança e interoperabilidade dentro e entre
todas as camadas que fazem parte da estrutura de comunicação. Isto é, deve ser possível utilizar equipamentos
de fabricantes diferentes para exercer uma certa função
e uma mudança de funcionalidade a um certo nível da
estrutura não deve implicar na mudança das camadas inferiores ou superiores”. |
|
 |
Para os conceitos de Indústria 4.0 a conectividade é fundamental, logo, todos os
protocolos são úteis. A ideia é que as coisas (devices) estejam conectadas, gerando dados
e que estes dados sejam utilizados de forma inteligente para gerar resultados melhores.
Neste momento é importante que cada responsável pela aplicação das tecnologias nas
empresas coloque seu time para identif car as oportunidades que os novos conceitos
estão trazendo e através destas busque melhorar os processos e obter as vantagens
destas tecnologias. |
|
|
Um objetivo da ampliação da conectividade nos ní-
veis superiores da estrutura de comunicação é permitir
que programas ou grupos de especialistas externas à planta possam oferecer serviços de otimização e manutenção.
Estes grupos podem fazer parte da corporação ou podem
se de empresas terceirizadas.
E à medida que os equipamentos são adicionados
ou substituídos, podem vir com sensores embutidos e o
sistema IIoT deve estar pronto para incluí-los. Jonas Berge
ressalta que aí se torna bem visível a vantagem de usar
padrões que vários fornecedores suportem porque se um
tipo específico de sensor não estiver disponível em um
fornecedor, pode-se obtê-lo em outro: mais sensores podem ser adicionados às redes
existentes desde que usem
o mesmo protocolo padrão
– isso é interoperabilidade.
Se qualquer sensor falhar, é
possível trocá-lo por outro
sensor de outro fabricante ou
ainda usar outro princípio de
medição, se necessário, desde que o novo sensor esteja
usando a mesma tecnologia
da rede – e então não será
necessário alterar os outros
sensores, o gateway de rede
ou qualquer um dos níveis mais altos da arquitetura IIoT, nenhuma programação é
necessária – no máximo uma mudança de configuração.
E esta é permutabilidade. É por isso que é tão importante
escolher um protocolo de rede de sensores digitais padrão desde o início e que ofereça um leque de escolhas
bastante amplo. |
|
 |
|
As redes de sensores digitais conectam os sensores
instalados nos equipamentos, em toda a planta, por isso
é importante usar padrões industriais que lidem com o
ambiente hostil e áreas perigosas e isso torna a IIoT especial. E importante evitar protocolos proprietários. Note
que nem wi-fi e nem toda Ethernet são usados no nível
dos sensores porque nem todos atendem aos requisitos
industriais, como segurança intrínseca e longa vida útil da
bateria. E note-se que há várias tecnologias de rede diferentes envolvidas em uma arquitetura IIoT: não é uma
única tecnologia; não dá para ser Ethernet e TCP/IP em
todo o caminho; não pode ser um protocolo, cabeado
ou não, por todo o caminho; e ressalte-se que IPv6 não
é necessário para os sensores em IoT. Como a rede de
sensores digitais está desacoplada das camadas superiores
(rede principal, segurança, nuvem e aplicativos etc.) da
arquitetura, é possível adicionar outro padrão de rede de
sensores no futuro se uma nova tecnologia mais poderosa
se tornar padronizada, como a Etherbus, ou mesmo para
migrar sensores para outras tecnologias de rede, sem ter
que fazer grandes mudanças ou substituir completamente
as camadas superiores da arquitetura.
No entanto, não misture padrões. As plantas tendem a usar o Foundation Fieldbus ou o Profibus-PA,
não ambos. Da mesma forma, apenas uma única rede
de sensores sem fio é necessária. A manutenção de duas
infraestruturas de rede sem fios semelhantes seria complexa e dispendiosa. Um gateway converte um protocolo
para outro, como o WirelessHart para o Modbus. Como
os sinais 4-20 mA ou on-off não são usados para estes
sensores adicionais, não há necessidade de conectar os
sensores para controlar as placas de IO do sistema. Os
sensores se conectam ao gateway, que por sua vez pode
se conectar diretamente ao historiador da planta ou ligarse à nuvem. E não há necessidade de substituir o sistema
de controle também. |
|
 |
|
Já existem sistemas de controle de processos que
passam informações via internet, em tempo real, sobre
diagnósticos de válvulas, transmissores, drives, etc. para
serviços especializados em manutenção ou otimização de
processo. O fundamento de toda essa iniciativa é a conectividade e a capacidade de converter grande volume
de dados em informação sobre o que fazer e como fazer
da melhor maneira. Tanto o Hart como o FF vêm oferecendo tudo que a indústria precisa em termos de riqueza
de dados, assim como o Modbus e o Profibus. Mas os
primeiros oferecem uma maneira mais objetiva e fácil de
obter os dados. “E acredito que o FF é o que mais se adequa, pois, o acesso é melhor estruturado e normatizado”,
ressalta Peluso.
Já os protocolos baseados em Ethernet (Profinet, Modbus TCP, Fieldbus HSE, Hart IP) não mudaram o como
os dados são organizados. Eles permitem mensagens com
maior volume de dados e a combinação de dados de diversos instrumentos, maior velocidade e uso da infraestrutura de rede. Como acontece com um gateway de um sistema WirelessHart: os dados enviados pelos instrumentos
através do WirelessHart são combinados em mensagens
usando Ethernet e TCP/IP que pode ser Hart IP, ModbusTCP, Ethernet IP, Profinet, etc. Da mesma forma, existem
acopladores ou link devices que recebem dados de redes
Profibus ou de blocos de entradas e saídas, e enviam via
Profinet. A novidade, se é que podemos considerar assim,
é o aumento da conectividade dentro e fora do ambiente
industrial, ferramentas analíticas para digerir os dados e
orientar o usuário.
Um gateway pode ser usado para sensores usados
tanto para monitoramento local quanto para controle de
processo, bem como para serviços IIoT. E sempre se pode
expandir o sistema IIoT sem ter que fazer grandes mudanças ou substituir completamente as camadas superiores
da arquitetura. E a rede principal conecta os gateways de
forma semelhante a uma rede do sistema de controle.
Ethernet e UDP/TCP/IP são usados como meio e transporte. Bom lembrar que existem muitos tipos de Ethernet
Industrial. Para preservar a riqueza dos dados do sensor,
deve-se usar a Ethernet Industrial correspondente ao padrão de protocolo usado para a rede de sensores.
O UDP / TCP / IP permite que múltiplos protocolos
coexistam no mesmo cabo Ethernet para que um backbone compartilhado possa suportar gateways de vários protocolos então, de novo: evite protocolos proprietários.
Uma vez que a rede principal está desacoplada das
camadas mais baixas (sensores e redes de sensores) e camadas superiores (segurança, nuvem e aplicativos, etc.)
da arquitetura, é possível adicionar outro padrão de rede
backbone no futuro.
E a segurança é um ponto crítico em tudo que se
conecte – existem várias opções para passar dados entre
as camadas e cada opção tem prós e contras. A solução
de segurança mais adequada pode ser selecionada dependendo do serviço fornecido e da arquitetura de automação da planta. O arquiteto de sistema do provedor de
soluções IIoT pode ajudar na melhor solução. |
|
 |
|
“Muita gente pensa que Indústria 4.0 significa uma
mudança total na base instalada e uma maneira totalmente diferente de desenvolver novos projetos. E há também
o falso conceito que Indústria 4.0 e IIOT são a mesma
coisa. Na verdade, o usuário pode começar a se beneficiar do novo conceito gradualmente, sem alterar a instalação ou trocar equipamentos existentes. Isto é possível
através do uso de programas que trabalham com o equipamento existente, proporcionam conectividade com a
rede interna e/ou global e trazem retornos à curto prazo.
É fácil e econômico adicionar novos pontos de medição
e controle através da inclusão de uma ou mais redes de
instrumentos wireless, Fieldbus ou Hart com fios. E não é
verdade que a nova onda requeira instrumentos de campo com endereço IP e ligados na Internet. Ainda que existam alguns instrumentos que possam ser conectados via
Ethernet, estamos distantes de ter todos instrumentos de
campo conectados por Ethernet. E esta Ethernet não será
como a que temos nos nossos escritórios e na indústria de
manufatura hoje”, afirma Jonas Berge.
Existem várias instituições internacionais estudando
o que precisa ser feito para que instrumentos de campo possam se comunicar com algo semelhante a TCP/IP,
usando dois fios para sinal e alimentação, cabos de longa
distância sem necessitar instalar chaves ou hubs em áreas
com atmosfera explosiva, vibração, temperaturas extremas, humidade e gases corrosivos, etc. Mas não será possível conectar essa “Ethernet” diretamente na rede local,
como muitos acreditam.
Por esta razão – e considerando que existe uma
enorme base instalada – a Indústria 4.0 vai trabalhar muito bem com todos os protocolos digitais existentes. Os
sistemas de controle, segurança e monitoração de ativos
funcionam como gateways entre os instrumentos ligados
a eles e as redes da planta, da corporação etc. OPC UA,
por exemplo, permite fácil transporte destes dados para
os mais diversos níveis das camadas superiores. O importante é que os protocolos de comunicação sejam abertos,
seguros, interoperáveis, robustos e flexíveis. |
|
 |
Eu diria que ninguém pode garantir a Indústria 4.0. Há muitos elementos importantes dela que
devem se unir para serem bem-sucedidos. Por exemplo, nossas tecnologias de barramento como
Hart e Foudation Fieldbus têm sido uma solução instalada em plantas de processo há mais de 20
anos. Do ponto de vista da Indústria 4.0, os usuários precisam apenas integrar essas informações
aos seus sistemas corporativos para efetivamente entrarem na era da Indústria 4.0.
Então, da nossa perspectiva, já permitimos a Indústria 4.0 desde os anos 90 através da
infraestrutura já que existe. Usuários e fornecedores de sistemas precisam apenas ter a
certeza de integrar esses barramentos em seus sistemas para que eles possam usufruir mais
dos dados. Este é outro elemento importante. Os usuários devem realmente usar o que têm.
Você pode conectar dispositivos inteligentes em sistemas inteligentes para que a informação
esteja disponível em todas as áreas da planta, mas se o usuário não olhar para os dados ou não
interpretar os dados para tomar melhores decisões e melhorar o seu processo, não há ganho,
todo o esforço é para nada. Para nós, esse é o maior obstáculo: mudar a maneira como as
pessoas operam. |
|
|
 |
Para atender os pilares conceituais da Indústria 4.0 é preciso utilizar
protocolos Ethernet industriais - ou seja, os protocolos fieldbus em suas
versões Ethernet. E eles precisam ser Ethernet tanto na comunicação dos
controladores com os sensores quanto na comunicação dos controladores
com os sistemas scada. A razão disto é que um dos pilares da Indústria 4.0 é
o IoT que prevê o empowerment da inteligência dos dispositivos de campo.
Uma das razões é esta. A outra razão é que conceitualmente a Indústria 4.0
se baseia na integração horizontal e vertical dos sistemas, o que se consegue
fazer num ambiente Ethernet Industrial de ponta a ponta, mas não com
protocolos industriais não Ethernet. |
|
|
“A conectividade aos níveis mais altos permite interação de sistemas até então estanques. Permite também a fácil integração com novas fontes de dados. E o
que observamos com wireless e o conceito de pervasive sensing. Fica muito fácil adicionar sensores e acessar
os dados destes sensores. Mas se por um lado ter muitos dados é bom, por outro lado você pode ser esmagado por eles. Como aconteceu com uma grande e
antiga empresa química, com diversas plantas nos EUA
e no exterior. A diversidade da base instalada é muito
grande: em várias destas plantas eles têm mais do que
uma geração de sistemas de controle, instrumentos de
vários fabricantes e de várias safras. Eles ainda têm instalados e operando os primeiros transmissores Hart.
Buscando melhorar manutenção de instrumentos e a
operação das diversas plantas, eles implantaram um plano
para acessar diagnóstico de todos instrumentos Hart, FF
e Wireless. E assim que os alertas de diagnósticos foram
ativados numa só planta, os operadores foram inundados
por mais de 3 mil alertas por dia. Isso sem contar com
os alarmes de processo. Era praticamente impossível gerenciar tudo isso. E a maior parte dos dados recebidos
era ininteligível para um simples mortal. Eu tive oportunidade de trabalhar com eles no problema e, através
de uma simples mudança no sistema de gerenciamento
de ativos, conseguimos filtrar alertas redundantes, repetitivos e irrelevantes. Houve uma redução de 85%
nos alertas. Os que sobraram foram os que são realmente importantes, requerendo algum tipo de ação. E
muitos dos alertas de instrumentos antigos vinham com
coisas como “alerta código 123 (???!!!)”. Alteramos o
texto para algo compreensível como “alta temperatura
na placa eletrônica” e textos explicando a causa provável e o que fazer a respeito. Depois da mudança, eles
conseguiram identificar e consertar muitos problemas
que poderiam causar paradas de alto custo, priorizar
manutenção, usar as informações para discutir com
fornecedores o melhor plano de ação etc. E também
conseguiram passar o diagnóstico de instrumentos mais
complexos para os especialistas do fabricante. A melhora no desempenho da planta foi surpreendente. Isso
ajuda a ilustrar que é possível trabalhar com os diversos
protocolos, de diversas gerações, minerando dados e extraindo informações valiosas e gerando recomendações
ou ações para um melhor rendimento. E como é possível
poder utilizar adicionar novas ferramentas que ajudem a
melhorar a produtividade e a segurança” finaliza Mestre
Marcos Peluso. |
|
 |
Na minha opinião, qualquer protocolo que utiliza o meio físico Ethernet
bem como os protocolos IP com a devida segurança da informação –
como confidencialidade, integridade, disponibilidade e autenticidade
entre outros - já garante o usuário na Indústria 4.0. Porém entendo
que tão importante quanto o protocolo de comunicação é a ferramenta
que irá ser responsável pela integração e gestão de todos os protocolos
existentes nas plantas e integração com os softwares de gerenciamento/
ERP/PIMS/BI, que preferencialmente devem contemplar os principais
protocolos industriais utilizados no mercado global para viabilizar o
acesso pleno e completo a Indústria 4.0. |
|
|
 |
Acredito que nenhum protocolo de campo específ co vai garantir a inserção do
usuário na Indústria 4.0. Embora a comunicação entre máquinas (M2M) e das
mesmas com sistemas de mais alto nível sejam fundamentais para o conceito de
Indústria 4.0, os protocolos de campo suportam troca de informações num nível
necessário, porém não suf ciente para que todos os recursos e benefícios da Indústria
4.0 sejam alcançados. Protocolos de mais alto nível, começando pelo OPC UA, serão
a base para a Indústria 4.0, e poderão ser implantados sobre diversos protocolos de
campo já existentes. |
|
|
 |
Em minha opinião, não é o protocolo utilizado que garante ao usuário a inserção
na Indústria 4.0, mas a forma como as informações são compiladas, modeladas e
reaplicadas ao sistema. É claro que alguns protocolos como Fieldbus Foundation e
Industrial Ethernet facilitam este trabalho. |
|
|
 |
Sem dúvida, as redes digitais facilitarão a inserção de usuários na Indústria 4.0 já que a palavra
chave é conectividade. Dentro deste cenário, eu vejo que o Prof net é o destaque porque
tem em sua arquitetura de comunicação mecanismos que permitem a abordagem sob a
perspectiva da Indústria 4.0: alta capacidade de desempenho em tempo real, topologias
? exíveis, disponibilidade, conectividade, diversos cenários, etc, tudo de forma objetiva e que
facilita a integração em rede, tanto na indústria de manufatura quanto de processo.
Prof net é, por enquanto, o único padrão que suporta a largura de banda completa em
tempo real e que atende aos requisitos de tempo e performance críticos. Ele já tem o conceito de segurança em vários níveis e, por
ser 100% Ethernet, também compartilha os desenvolvimentos de segurança futuros do mundo de TI. Some-se a isso a conf abilidade
operacional e a disponibilidade - palavras-chave na operação de uma da planta. Acredito que no médio e longo prazos todas as
tecnologias atenderão a isto, porque precisam dar suporte a estruturas de redes digitais e Ethernet. A Indústria 4.0 já é uma conexão
lógica de todos os dispositivos e meios relacionados ao ambiente produtivo em questão - os sensores/atuadores, transmissores,
estações de computadores, células de produção, sistema de planejamento produtivo, diretrizes estratégicas da indústria, informações
de governo, clima e fornecedores. Todos os dados sendo aquisitados online e analisados em um banco de dados. Mas para que isto
possa acontecer, os sistemas de automação devem estar orientados ao aumento da produção, redução de custos e visão nas mudanças
tecnológicas, e para isso a plataforma tecnológica deve estar estruturada com redes industriais, equipamentos inteligentes e com
diagnósticos, sistemas de otimização e um banco de dados. |
|
|
 |
Os padrões de redes industriais estão carregados de informações dos instrumentos
e controladores industriais. Todos esses dados poderão ser usados na integração de
sistemas para a indústria 4.0. O grande desaf o é como realizar a integração de diversos
componentes, com tantos padrões de protocolos diferentes utilizados pelo mercado de
automação. Um dos protocolos de grande aceitação é a Ethernet Industrial - que também
tem diferentes padrões: EtherNet/IP, Modbus TCP, Prof net. Com o IPv6, a Ethernet é
um protocolo em grande expansão para redes cabeadas e sem f o. Ainda há outros
protocolos com soluções robustas para o meio industrial, como o ZigBee, que permite o
desenvolvimento de dispositivos integráveis a conceito de IIoT e M2M. |
|
|
 |
Essa discussão ajuda a f xar os conceitos que chegam com a Indústria 4.0, a
indústria de 4ª geração, que está ainda em um processo de desenvolvimento
- mas a passos acelerados, como ocorre com os processos tecnológicos. Desde sua
primeira revolução, a indústria vem se reinventando, primeiro com a utilização
da força do vapor e da água para diminuir o trabalho braçal, mecanizando
processos. Depois foi o momento de aumentar a produtividade, conceito muito
bem desenvolvido pela linha de montagem de Henry Ford. O terceiro passo foi
a digitalização com o desenvolvimento dos “smart devices” e dos protocolos
industriais. E a indústria 4.0 integra conceitos novos como Iot (Internet of Things) ou
IoE (Internet of Everything) e Big data. Daí nasce a expressão indústria conectada,
trazendo para linha de produção ou plantas industriais agilidade, versatilidade e, consequentemente, produtividade. Quando falamos
sobre Foundation Fieldbus, Prof bus, Devicenet ou Asi-Bus, nos reportamos à geração anterior. Esses protocolos e a sua tecnologia
estão instalados mundo afora integrando desde dispositivos de campo até células industriais. Os desenvolvedores trabalharam
para atender os conceitos de protocolo aberto e interoperabilidade e f rmaram uma enorme base instalada. Mais recentemente
surgiu a Industrial Ethernet, que aproxima ainda mais a manufatura e sistemas de controle da tecnologia da informação. Foram
introduzidos dispositivos wireless, trazendo a expectativa de uma maior versatilidade e a diminuição de infraestrutura para
instalação de instrumentos. Vi num primeiro momento a resistência de consumidores e até de prof ssionais, apreensivos com
relação a aspectos tais como integridade de baterias e dos sinais transmitidos em ambiente industrial, tipicamente repleto de
interferências eletromagnéticas. Os protocolos industriais existentes podem, cada um à sua maneira, fazer parte da Indústria 4.0,
desde que integrados aos novos conceitos. Não haverá um protocolo mais adequado. Serão necessários ajustes nas tecnologias para
torná-las ainda mais próxima da Tecnologia da Informação, uma das bases da indústria 4.0. Mas ouso af rmar que, depois da barreira
tecnológica, haverá um árduo trabalho de convencimento dos usuários para alterar toda a sua base instalada. Exemplo recente disso é a
utilização da tecnologia analógica: com a chegada dos “smart devices”, os instrumentos 4-20mA estavam condenados, desapareceriam
da indústria, no entanto, como prof ssional de projeto ainda especif co instrumentos que transmitem esse tipo de sinais, atendendo a
critérios dos clientes. |
|
|
 |
Claro que os protocolos Fieldbus Foundation, Hart, Prof bus, Devicenet e outros
fazem parte da inserção dos usuários na Indústria 4.0. Quanto mais dispositivos
conectados online, mais dados, quanto mais dados, mais informações, quanto
mais informações, mais conhecimento. Quanto mais conhecimento, mais decisões
assertivas tomaremos na indústria. |
|
|
 |
A maioria dos protocolos possibilita a troca de informações entre os diversos
níveis de automação, porém, para que se implemente a Automação 4.0, a troca de
informações entre os sistemas existentes e os usuários é importante, e a estrutura
da base de dados de TA e TI é que vai determinar o nível de informação requerido.
Mas acredito que as redes Ethernet e Prof bus são as redes com maior possibilidade
de disseminação de uso para a implantação da Indústria 4.0. |
|
|
 |
O fato é que para a Indústria 4.0 acontecer de verdade e de forma prática, torna-se
necessário um backbone de comunicação que permita a comunicação e a integração
(vertical e horizontal) entre os componentes do ecossistema que compõem a Indústria
4.0. Esse backbone e a forma como esse ecossistema interage entre si é conhecido como
IIoT (Industrial Internet of Things). Dada a característica multivendor de um sistema de
Indústria 4.0, não é 100% possível af rmar que apenas um único protocolo poderá prover
todas as funcionalidades requeridas por diferentes equipamentos e sistemas instalados
em diferentes níveis da indústria. Nesse sentido, um sistema de IIoT deve ser capaz de
atender desde as exigências extremas de desempenho do chão de fábrica à enorme
quantidade de dados necessários em sistemas de corporativos. Isso sem abrir mão de
funcionalidades como conectividade, interoperabilidade, alta disponibilidade, recursos de segurança e conf dencialidade. Essa é a razão
pela qual muitas literaturas, whitepapers e guidelines apontam o Prof net e o OPC-UA (trabalhando em conjunto e extraindo o melhor
de cada um deles) como o verdadeiro backbone da Indústria 4.0. Ambos os protocolos são 100% baseados em Ethernet e acompanham
a evolução das redes Ethernet conforme os novos padrões de TI vão surgindo, como Gigabit Ethernet, redes TSN, modelos otimizados
de troca de dados, padrões de segurança, etc. Isso tudo, sem se esquecer da integração dos equipamentos e sistemas legados em uso,
assim como a integração com outros protocolos não Ethernet e que certamente farão parte de um ecossistema de Indústria 4.0, como os
protocolos AS-i e IO Link. Daí a importância da escolha dos melhores protocolos ou suíte de protocolos que irão compor esse IIoT. |
|
|
 |
Dentro do conceito da iniciativa Industrie 4.0 , o protocolo adotado é o OPC-UA, que
tem se mostrado o melhor para a padronização na troca de dados entre os agentes
envolvidos no processo produtivo e a nuvem (e vice-versa). Dessa forma, todos os
dispositivos, ou agentes (por exemplo: máquinas, robôs, impressoras, etc), num
processo de produção, visando atender aos requisitos da iniciativa Industrie 4.0
deverão ser capazes de realizar troca de dados através do OPC-UA.
Portanto, os demais protocolos não foram adotados como padrão na iniciativa Industrie 4.0.
O conceito da automação baseada em PC, que é a tecnologia difundida pela BECKHOFF por
mais de trinta anos, mostrou-se a mais adequada na adaptação às necessidades da iniciativa
Industrie 4.0 por diversos motivos, entre eles a adequação fácil e imediata na utilização
dos padrões OPC, diferentemente do que ocorre com os PLCs tradicionais. Dessa forma,
considerando fatores como interoperabilidade, segurança de dados e escalabilidade o padrão
OPC-UA garantirá a inserção de usuários na iniciativa Industrie 4.0. |
|
|
 |
|
 |
|
 |
“O entendimento da Vale é que para os protocolos baseados em Ethernet Industrial, como por
exemplo o Fieldbus HSE e o Prof net, a inserção nos conceitos da indústria 4.0 seja possível,
uma vez que nestes casos teremos condições de garantir que os componentes e equipamentos
industriais sejam capazes de gerar informações além dos tradicionais diagnósticos de falhas
e monitoramento de funcionamento, como por exemplo implementar automaticamente
predição de falhas, abertura de ordens de manutenção e até mesmo se comunicar entre
si. Numa camada de gestão da informação, acima das plantas industriais, tais protocolos
facilitariam o envio das informações para uma infraestrutura centralizada, preferencialmente
em cloud, onde mecanismos de Big Data Analytics poderiam ser utilizados para identif car
padrões de falha e de performance operacional , comparar variáveis e equipamentos entre
diversos sites e, com isso, oferecer feedback em tempo próximo do real para que operadores e analistas possam garantir a melhor ef ciência,
performance e disponibilidade dos equipamentos do parque industrial. Tais protocolos, baseados em Ethernet, possuem alta taxa de
transmissão e podem atender tanto aos requisitos usuais de tempo real em áreas industriais (ciclos inferiores a 10ms), quanto aos equipamentos
que não necessitem de resposta em tempo real (ciclos de atualização superiores a 100ms) utilizando, nesse último caso, a pilha TCP/IP.
Nas plantas construídas mais recentemente temos priorizado a instalação de sensores, componentes e equipamentos baseados em protocolos
TCP-IP industrial. No caso dos protocolos mais antigos, como Hart, Prof bus e DeviceNet, entre outros, haveria maior dif culdade nessa
inserção, uma vez que, embora rápidos na transmissão dos dados pelo enlace, são mais restritos quanto ao set de informações que podem
ser transmitidas ou em funcionalidades de interações. Assim, estes protocolos apresentam maior dif culdade para acomodar o aumento de
mensagens e atividades que ocorreriam na rede de automação para atender à Indústria 4.0 e também necessitariam de algum tipo de gateway
para transformar os dados gerados e enviá-los a alguma cloud para análise centralizada. A visão da Vale é de implementar um Data Lake de
dados industriais, através de uma plataforma de IIoT de modo a conectar suas unidades de negócio e viabilizar a utilização de ferramentas de
análise de dados para gerar informação e conhecimento embasado. Isto nos permitirá entender melhor o comportamento de um equipamento
ou processo, sua tendência, predizer falhas, aprimorar a integração da cadeia produtiva e das unidades de negócio, melhorar a gestão de ativos,
atividades de manutenção, informações de capacidade, disponibilidade e ef ciência dos ativos. Todas estas iniciativas estão conectadas com
a agenda de transformação digital da Vale e visam contribuir, de forma segura e sustentável, para aumentar a produtividade, reduzir custos e
aumentar lucratividade. ” |
|
|
 |
Para entender se a utilização de redes - Fieldbus Foundation, Hart, Prof bus, DeviceNet
e outros protocolos - pode garantir a inserção dos usuários na Industria 4.0, é preciso
analisar alguns pontos e conceitos: A Indústria 4.0 possui três pilares: Industrial Internet of
Things (IIoT), Cyber Physical Systems (CPS) e Smart Digital Manufacturing (SDM). Quando
olhamos por esta perspectiva, apenas a utilização de redes como Fieldbus Foundation,
Hart, Prof bus e DeviceNet não garantem a inserção ou a infraestrutura necessária para a
jornada da construção da Indústria 4.0, uma vez que esta iniciativa se apoia na utilização
de dispositivos industriais com conectividade em Ethernet. Por outro lado, o objetivo da
Indústria 4.0 é coletar dados, analisar seu contexto, predizer uma tendência e adaptar o processo para sua otimização ou prevenção de
uma falha. Quando olhamos para o cenário industrial, cujos ativos costumam ter um ciclo de vida de dez, vinte anos ou mais, temos
uma realidade muito diferente da área de Tecnologia da Informação, cujos os ativos costumam ter um ciclo de vida de 5 anos. Neste
cenário de longevidade, e tendo em vista a realidade da indústria brasileira, não é algo factível e realista realizarmos toda a substituição
dos dispositivos industriais ou aguardar o termino de seu ciclo de vida para que então possamos iniciar a jornada rumo a Industria 4.0.
Podemos tirar proveito dos dispositivos existentes, através de redes e protocolos de comunicação que sejam a Ethernet, desde que
utilizemos CLPs, PACs e SDCDs com capacidade de integração de diferentes redes e diferentes protocolos até a rede Ethernet, permitindo
assim uma integração vertical e horizontal de toda a cadeia produtiva. Então é possível garantir a inserção de usuários de redes como
Fieldbus Foundation, Hart, Prof bus, DeviceNet e outras na manufatura 4.0, desde que se escolha a tecnologia correta de controle
industrial, af m de garantir uma arquitetura integrada do sistema de automação e controle com outros níveis da cadeia produtiva. |
|
|
 |
Quando falamos em Industria 4.0, conceitualmente faz-se obrigatório a conexão dos
equipamentos (automação, shop ? oor) com o ambiente interno (prória empresa até nível ERP)
e também externamente (condições climáticas, monitoramento em real-time, tendências
sociais/governamentais, economias, etc), trazendo o conceito bem forte como IoT, Cloud e Big
Data + Analytics. Primeiramente para o nível de Shop Floor, acredito que a tendência será irmos
para Prof net e subindo para ERP podemos usar protocolos B2MML com base na norma da ISA
95. Assim, trazendo as informações com conectividade externa, acredito que teremos em breve
protocolos e normas mais bem def nidas para IoT e Cloud, porém hoje já vemos 3G, 4G, GPRS,
tecnologia com APIs e conectividade com satélites. |
|
|
 |
Considerando que no conceito da Indústria 4.0 os componentes de uma fábrica/processo industrial
estarão cada vez mais conectados (desde os mais simples sensores aos mais poderosos mainframes),
os dados coletados por cada componente poderão trafegar por toda a planta industrial, tem-se que
quanto mais informações possam ser coletadas/transmitidas, mais eficaz/eficiente o processo de
fabricação pode se tornar. Umas das ideias principais por trás desse conceito é a dita “comunicação
de feedback” entre as máquinas e as pessoas: as próprias máquinas passam a “dizer” como elas estão
sendo usadas e/ou quando há uma necessidade iminente de reparo. Essas informações não só poderão
ser utilizadas pelo usuário/equipe de manutenção, como também pelo próprio fabricante da máquina
que poderá, então, otimizar todas as fases do processo de produção, de fornecimento, desenvolvimento
e criação, poupando assim, tempo e dinheiro. Para compreender bem como tudo isso pode funcionar,
é necessário o entendimento de dois conceitos importantes: Cloud Computing e Internet-of-Things (IoT). A primeira refere-se à hospedagem de tudo
na internet (nuvem), o que permite o acesso remoto a aplicativos, dados e serviços em qualquer parte do mundo. Já o segundo, refere-se a qualquer
dispositivo eletrônico estar conectado à nuvem, enviando/recebendo dados de/em qualquer lugar da galáxia (lembre-se da estação espacial e das
sondas espaciais enviadas para outros planetas) No conceito da indústria 4.0, tanto a Cloud Computing quanto a Internet-of-Things (IoT) são utilizadas
para processar as informações que normalmente são gerenciadas internamente por pessoas/máquinas e então, movê-las para a nuvem,onde possam
ser gerenciadas de qualquer lugar do mundo. No entanto, essa interligação entre máquinas e/ou processos a fim de permitir a maximização da troca de
informações só é possível caso existam barramentos de dados compatíveis com essa vultosa quantidade de informação. É através desses barramentos
que as informações trafegam entre os diversos dispositivos, agora, geograficamente distantes. Assim, no ambiente industrial, háa necessidade cada vez
maior do desenvolvimento de protocolos fieldbus capazes de trabalhar com grandes quantidades de dados, em alta velocidade e com segurança. Nesse
contexto, os barramentos Fieldbus Foudation, Profibus e Devicenet ganharam destaque nos últimos anos por permitirem uma troca de dados rápida entre
os equipamentos da rede industrial, mas estão sendo paulatinamente substituídos por barramentos de dados que utilizam o padrãoEthernet, os ditos
protocolos RTE - Real Time Ethernet. São eles: Profinet, Ethernet/IP, HSE, Ethercat, entre outros. Além de mais rápidos, os protocolos baseados no Ethernet
permitem uma troca de dados mais transparente entre as diversas camadas da pirâmide da automação, permitindo assim uma maior integração tanto
horizontal quanto vertical entre os dispositivos. Assim, acredito que os protocolos Fieldbus Foundation, Hart, Profibus, Devicenet e outros não podem,
por si só, garantir a inserção dos usuários na Indústria 4.0, mas vão ao encontro dessa nova realidade, e, não só poderão, comdeverão ser utilizados como
suplementos das novas redes RTE em casos específicos como em áreas classificadas e/ou com infraestrutura de rede já instalada. |
|
|
 |
Em minha opinião, como a Indústria 4.0 ou Quarta Revolução Industrial é a definição de um termo que
engloba algumas tecnologias para automação e utiliza conceitos de sistemas ciber-físicos, Internet das
Coisas e computação em nuvem, os diversos protocolos existentes poderão facilitar, por exemplo, as
configurações de instrumentos, recuperação destas configurações e agilidade no processo de manutenção
e calibração de instrumentos com estes protocolos, na indústria. Também acredito na significativa redução
de papéis, como Datasheet, folhas de configuração e certificados de calibração, já que estes dados poderão
estar na nuvem, em fácil acesso e recuperáveis. Acredito que com estes protocolos será potencializada a
inserção dos usuários na Indústria 4.0, pois eleva-se a capacidade de configuração e operação em tempo
real de instrumentos, que consiste na aquisição e tratamento de dados de forma instantânea, permitindo
a tomada de decisões rápidas e com agilidade. A orientação a serviços, com a utilização de arquiteturas de
software orientadas a serviços aliado ao conceito de Internet of Services. E para finalizar a modularidade,
que oferece flexibilidade para alterar as tarefas das máquinas facilmente. |
|
|
|
|
|
LEIA MAIS
NA EDIÇÃO IMPRESSA |
|
DESEJANDO
MAIS INFORMAÇÕES: redacao@editoravalete.com.br
|
|
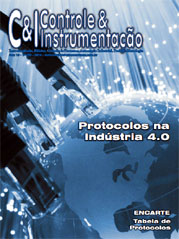 |
Clique na capa da revista para
ler a edição na íntegra |
|
|