Revista Controle & Instrumentação Edição nº 213 2015
|
|
¤
Cover Page
|
Protocolos de Comunicação devem ajudar a indústria
a ingressar na IIoT |
|
|
 |
|
Éconsenso que o futuro dos protocolos de comuni- cação está no Ethernet. Ainda que muitos projetos utilizem Fieldbus, Profibus e suas variantes, o parque instalado é dominado por 4-20mA com Hart – e os
fornecedores de tecnologia ainda lançam produtos para
esse nicho. “Cerca de metade da base instalada de todos
os dispositivos de campo no mundo são Hart. Dispositivos FF provavelmente cheguem a 15%. Então você tem
outros protocolos de campo, como Profibus PA, que tem
uma quota de mercado ligeiramente menor que do FF.
E o Ethernet IP ainda tem uma base instalada realmente
pequena. Mas vem novidade por aí. A tecnologia APL traz
a Ethernet até o dispositivo e tem o
potencial de substituir a camada
física de ambos os protocolos FF e
HART. APL, na minha opinião, é a
peça final do quebra-cabeça que
vai trazer a tecnologia Ethernet para
os dispositivos de campo e automação de processos”, confirma Larry
O’Brien, vice-presidente de pesquisa do ARC Advisory Group.
“O alto parque instalado de dispositivos com redes
4-20mA com HART não impede que a empresa se ajuste aos novos conceitos, como IIoT, Indústria 4.0 ou o
Connected Enterprise; porém, a tendência de convergência para redes IP nos direciona a adotar esta tecnologia para projetos futuros”, comenta Raul Groszmann, da Rockwell
Automation.
“Se utiliza, sim, muito 4-20mA
mas o mundo é digital, fala-se em
cloud e IIoT então é preciso melhorar o digital e nossa relação com
ele, não podemos ficar satisfeitos
com o mundo analógico. A instrumentação digital não pode ser
descartada em função da dificuldade de instalação ou
de compatibilidade porque ela é rica de informação que
nos faz mais produtivos de maneira segura”, afirma o representante oficial da Petrobras no grupo de usuários do
Fieldcomm Group, Miguel Borges,
engenheiro de equipamentos Senior do Cenpes/Petrobras e responsável pelo Lead - Laboratório de
Controle e Automação, Engenharia
de Aplicação e Desenvolvimento.
“Quando falamos em implantação de novos projetos de instrumentação temos de considerar algumas variantes, a primeira delas
é em que lugar do pais será implantada a nova planta.
Teremos mão de obra qualificada para: operar, dar manutenção e atualizar a tecnologia a ser implantada? Temos
Protocolos de
Comunicação devem
ajudar a indústria a
ingressar na IIoT
Emerson
Controle & Instrumentação Nº 213 | 2015 41
tido experiência de muitas vezes o cliente querer os 4 a
20 mA e sequer aceitar o protocolo Hart, devido ao fato
de não ter mão de obra qualificada. Outro problema
que enfrentamos é que temos um excesso de formação
de novos profissionais em automação industrial, porém
não temos formação em instrumentação de chão de
fábrica. E isto é sério, formamos profissionais de automação sem a base de campo. Quanto aos protocolos,
temos hoje uma tendência ao Profibus DP ou PA e as redes Profinet.
Devemos isso ao excelente trabalho de divulgação dos fabricantes
e a Fundação Profibus. No caso da
Fieldbus Foundation não vemos
um trabalho de divulgação da tecnologia, independente do mérito
da associação ou conjunto de fabricantes”, afirma Marcílio Pongitori, diretor da ISA Campinas.
Paulo Borges Campos, gerente de aplicações da Borges Katayama, ressalta, em complemento ao
exposto, que existem outros fatores que podem colocar em risco a
confiabilidade dos equipamentos
eletrônicos, independentemente do fabricante e da tecnologia
a ser aplicada em cada processo industrial. “Os novos
equipamentos eletrônicos estão sofrendo com a norma
RoHS, que elimina dos novos circuitos eletrônicos os
metais pesados como estanho e chumbo, o que acaba
afetando todos os fabricantes”. E isso merece uma edição especial!
História de acertos e
tropeços
Mas, para decidir sobre um
protocolo, Harry Forbes, analista
sênior do ARC Advisory Group,
recomenda que os usuários finais
considerem vários fatores, mas de
um modo geral os mais importantes seriam: o portfólio de produtos
disponíveis em uma determinada
rede de campo, a facilidade de gerenciamento dos dispositivos de campo, e o suporte durante o longo ciclo
de vida que esses dispositivos geralmente têm. “Os dispositivos Hart ainda dominam o mercado, mas a maioria deles não tem sua característica Hart usada continuamente. E termo “Ethernet” não se refere a uma única
tecnologia, e sim a um grande conjunto de camadas físicas e de enlace de dados que foram padronizadas sob
o standard IEEE 802.3. É por isso que temos Ethernets
com 10 MB, 100 MB, Gigabit, Fibra Óptica, etc. Este
conjunto de padrões cresce a cada ano, mas nós ainda
chamamos todas essas coisas de
Ethernet. É preciso atenção”
O consultor e professor
Augusto Passos Pereira lembra
que precisamos analisar os protocolos digitais de campo olhando o
futuro e não o passado. O Hart,
quando surgiu, tinha como objetivo permitir a utilização do sinal
4-20 mA para a informação de
processo e a frequência do protocolo para permitir a
configuração e parametrização de dispositivos de campos como transmissores e posicionadores de válvulas.
Na sequência vieram os softwares de diagnósticos, e o
desenvolvimento de vários softwares que realizavam
estas funções, ao contrário do que se imaginava, proporcionou maior popularização das vantagens do uso
do protocolo, o que acabou numa guerra entre os fabricantes, um jogo de esconde-esconde aonde algumas
informações de diagnósticos ficavam atreladas ao uso
de um software em particular.
Na sequência do tempo surgiram Profibus DP que
foi desenvolvido para interligar através de uma rede de
campo inicialmente os inversores de frequência, sensores de posição, botoeiras de acionamento, válvulas
on-off e outras funcionalidades.
Mas os usuários já naquela época ficavam frustrados pois as plantas rodavam com uma determinada
marca, mas, numa troca de dispositivos vinha a dificuldade de uso dos diagnósticos e de configuração -
dificuldade não resolvida até hoje. A compatibilidade
dos diagnósticos entre as diversas marcas de software
também aconteceu, e teve início a era do diagnóstico
avançado.
No início dos anos 1990 surgiram o Fieldbus Foundation e o Profibus PA desenvolvidos para as redes de
interligação dos transmissores das variáveis de processo
e os posicionadores das válvulas de controle. E a mesma
situação repetida em relação aos softwares de configuração e diagnóstico aonde a diferença de marcas trazia
o problema de qualidade e quantidade dos diagnósticos.
“Os protocolos Hart, Fieldbus Foundation e Profibus PA foram desenvolvidos para aplicações semelhantes - transmissores e válvulas de controle - e o Profibus
DP para aplicações de pontos discretos e no projeto dos
CCMs inteligentes envolvendo os inversores de frequência, partidas eletrônicas, botoeiras e válvulas on-off. Então, quando pensamos em convergência devemos levar
em conta estes conceitos”, frisa Augusto, ressaltando o
fato das fundações Hart e Fieldbus resolverem ter uma
atuação conjunta: as empresas e pessoas envolvidas
são as mesmas. “Existe muita sinergia de trabalho, mas
não há condição de convergência da utilização destes
protocolos pois eles têm aplicações distintas. Pode ser possível no futuro um novo protocolo vindo da fusão do
Profibus PA e do Fieldbus Foundation, e também entendo que o sinal 4-20 mA + Hart ainda tenha uma sobrevida considerável pois requer uma capacitação menor
das pessoas que lidam com ele”, diz Augusto.
Usuário precisa de mais segurança
“Mas é bom ressaltar”, diz Marcílio Pongitori, “que
apesar do tempo de utilização do 4-20mA com Hart,
ainda nos deparamos com plantas onde este protocolo
é subutilizado pela pouca familiaridade dos profissionais de instrumentação com protocolos digitais. E com
relação as redes Ethernet Industriais no chão de fábrica,
vejo que as novas gerações vão desenvolver soluções
utilizando este protocolo dada a sua difusão e aplicação
em outras áreas”.
Ronaldo Neves Ribeiro, gerente do Departamento de Tecnologia da Informação e Telecom da
Cenibra pontua que o mais importante é pensar na segurança. “Nós,
usuários de tecnologia, ainda não
estamos totalmente seguros com o
Ethernet no chão de fábrica, embora saibamos que funciona em
todos os demais lugares. Olhando
pelas instalações, ainda temos dificuldades com elas
no meio industrial. Geralmente instalações adequadas
para um bom funcionamento das redes custam mais
caro e nem todos os projetos estão dispostos a investir nisto. Logo, naturalmente gera uma ação de fazer
como sempre foi feito e assim é mais fácil usar o Hart
mais 4-20mA. Já na decisão de usar o FF, Profibus ou
outro protocolo, há a necessidade de cuidados especiais
que geralmente não são observados, trazendo fracassos
em alguns projetos. Há ainda a dificuldade de treinar os
montadores que estão acostumados com o formato antigo e demoram para se especializar na nova realidade”.
Mas nem todos os usuários têm medo de usar outras tecnologias além de Hart com 4-20. Segundo Larry O´Brien, Saudi Aramco, Shell e BP realizaram uma
demo de FF – SIF, FF para aplicações de segurança.
Aparentemente, foram apenas testes. Mas já é um começo. Assim o receio de usar novas tecnologias vai sendo vencido em várias frentes.
“Mas os usuários realmente ainda não estão totalmente seguros com o Ethernet no chão de fábrica, embora saibamos que funciona em todos os demais lugares.
Instalações adequadas para um bom funcionamento das
redes custam mais caro e nem todos os projetos estão
dispostos a investir nisto, logo, gera uma ação de fazer
como sempre foi feito e como é mais fácil: Hart com 4
a 20. A decisão de usar o FF, Profibus ou outro protocolo, demanda cuidados especiais, geralmente não observados e isto tem trazido fracassos em alguns projetos.
Há ainda a dificuldade de treinar os
montadores que estão acostumados
com o formato antigo e demoram
para se especializar para a nova realidade”, comenta Harry Forbes.
Tomé Guerra, especialista em automação da Pöyry Tecnologia, concorda que existem dificuldades mas
ressalta que a tecnologia Ethernet
tem sido bem usada na interligação entre estações de
operação/servidores, controladores/CLPs, módulos de
comunicação/gateways e tem a grande vantagem da velocidade e facilidade de uso com switches para gerenciamento das redes. “Já na ligação com os instrumentos e
sensores de campo os protocolos FF/HART/Profibus-PA/
ASI/etc ainda prevalecem, até porque o Ethernet tem a
limitação de distância e alimentação para o instrumento
porque mesmo usando o POE do cabo não atende o
consumo em alguns casos. A restrição da distância pode
ser eliminada com o uso de cabo de fibra ótica, porém
ainda continua o problema de ter de levar alimentação.
Existe, até dependendo da aplicação, a opção do HartIP usado para conexões com instrumentos via wireless
e gateways, que permite transferir diagnósticos para gerenciamento de ativos. O nível de automação da planta
e seu processo determinam as aplicações, escolha de
tecnologias, escolha de I/Os locais ou remotos, classificação de área e nível de topologia na ligação de rede
até a sala de controle, pois apesar de se usar Ethernet
como meio físico alguns fornecedores ainda mantém
um protocolo proprietário no nível de aplicação da camada OSI (exceção para os protocolos abertos como
ProfiNet, Ethernet-IP, etc.) ”.
“Ethernet e Hart e FF não são mutuamente exclusivas. Ethernet é uma tecnologia de camada física”, lembra Larry O´Brien.
Mestre Marcos Peluso, distinguished technologist Emerson,
destaca que aplicação de protocolos de comunicação baseados em
Ethernet vem crescendo bastante
em alguns setores da automação
industrial. Na manufatura, é muito
comum encontrar diferentes tipos
de Ethernet sendo utilizados para
comunicação entre CNCs, PLCs e
blocos de entrada e saída de sinais discretos e analógicos, câmeras de vídeo, etc. Já na indústria de controle
de processos, o uso de Ethernet fica praticamente restrito às redes dos sistemas de controle e alguns instrumentos de medição mais complexos como analisadores de
gases. O uso de Wi-Fi em plantas vem se popularizando, permitindo o acesso a câmeras de vídeo, operador
móvel, monitoração de presença de pessoal, etc. Por
razões de segurança, Wi-Fi é normalmente conectado aos níveis superiores da rede de controle, isolados através de firewalls.
“Mas a comunicação predominante entre os instrumentos de campo e os sistemas de controle ainda
é o velho 4-20 mA. Ainda que o protocolo de comunicação Hart esteja disponível em praticamente todos
os instrumentos de campo em 4-20 mA, somente uma
pequena porcentagem dos usuários utiliza as vantagens
oferecidas pela comunicação digital. E a maioria daqueles que decidiram utilizar protocolos puramente digitais
como Foudantion Fieldbus ou Profibus, não tiram vantagens dos benefícios que a tecnologia oferece. O que
acontece com os instrumentos inteligentes é mais ou
menos o que acontece com o indivíduo que comprou
um Iphone e só o utiliza para telefonar. Como a maioria
dos proprietários de Iphones fazem amplo uso dos aplicativos que dispositivo oferece, fica a pergunta: por que
o mesmo não ocorre com os instrumentos inteligentes?
O que temos observado é que o primeiro problema está
na falta de tempo. No caso de instrumentos 4-20 mA, é
relativamente fácil conectar o instrumento de campo ao
sistema de controle e ter algum valor para a medição. O
valor pode não ser muito preciso por falta de calibração,
acerto de zero, condensado ou gás na linha de impulso,
erro causado por interferência eletromagnética etc. Mas
se o erro não for gritante, o pessoal convive com ele.
Configuração de diagnósticos e outras funções é normalmente deixada para depois. E nunca mais ocorre. E
aí vem o pior: como o instrumento não foi configurado
propriamente, o operador pode ser bombardeado por
alarmes inexpressivos e incômodos. Outro problema
muito comum é com a instalação elétrica. Se a instalação não é bem-feita, o 4-20 mA pode operar sofrivelmente, mas ainda assim ser utilizado. Já a comunicação
digital Hart pode ser comprometida pelo ruído elétrico,
gerando uma porção de alarmes de erros de comunicação. Alarmes causados por má configuração e por falhas
de comunicação podem encher páginas e mais páginas
do log de alarmes e deixar o operador muito mal-humorado. Também por falta tempo ou conhecimento,
instrumentos com Fieldbus e Profibus acabam sendo
configurados para praticamente só oferecer o valor da
medição. E como a comunicação é puramente digital,
problemas de instalação exigem atenção imediata. O
problema do conhecimento e falta de tempo tem várias facetas. Empresas cortaram o número de técnicos
especializados drasticamente e alocaram muito pouco
tempo para treinamento dos remanescentes. Qualquer
planta tem uma grande variedade e número de instrumentos, o que dificulta um conhecimento mais aprofundado das características de cada um. E para piorar, a
maioria dos fabricantes de instrumentos não colocaram
muito esforço em fazer com que estes instrumentos sejam fáceis de configurar e operar.
E, infelizmente, observamos uma considerável
queda na qualidade do pessoal técnico disponível.
Este é um fenômeno global. Erros básicos de projeto
e instalação acabam desviando muitos recursos, não
permitindo que as pessoas tenham tempo para ganhar
tempo. Um pouco de treino, cuidado com a instalação
ajudam a economizar muito tempo e dinheiro”, diz
Mestre Peluso.
“Temos uma situação óbvia que, em minha opinião,
é de desapontamento com a incapacidade da nossa indústria se unir para determinar a melhor forma de utilizar as novas tecnologias para o serviço do nosso mercado. O que vemos são promessas e expectativas não
cumpridas. Cadê a interoperabilidade e intercambiabilidade que eram promessas do Fieldbus? Esquecidos. O
que era para ser simples transformou-se em complicado
– cálculos de micro-ciclo?!! Engenharia de topologia de
ramos e troncos?!! Falhamos em oferecer soluções ao
mercado. No lugar disso oferecemos uma interminável
guerra de padrões que nada mais que são que tentativas
de converter o princípio dos padrões em ferramentas
de marketing. Meu padrão é melhor que o seu. Marketing posto acima da tecnologia. Enquanto as cabeças
da indústria conduzem as guerras de marketing, nossa indústria vai absorvendo as tecnologias disponíveis
de outras áreas e utilizando-as da melhor forma para
atender as suas necessidades. Portanto temos uma larga
utilização de Ethernet como parte integrante da todas
as camadas de comunicação dos sistemas de controle
- menos a camada de campo. Não há uma “padronização” propriamente dita dessa utilização. Existe uma
prática “de fato” em cima da qual “melhores práticas”
estão surgindo para que possamos utilizar essa tecnologia sem comprometer a segurança de informação, a disponibilidade, a susceptibilidade a problemas externos e
assim por diante. Os protocolos de campo como Hart,
Fieldbus e Profibus e Wireless permanecerão como tais
– de campo e não vão expandir o seu campo de aplicabilidade além dessa fronteira. O mercado continuará
fragmentado entre esses diversos protocolos em função de dois fatores muito fortes: em primeiro, nenhum
deles se mostrou tão superior ao outro que justificasse
uma migração em massa para o seu lado. Em segundo,
nosso mercado mundial está parado, não há uma atividade forte de construção de novos complexos industriais (pelo menos nas áreas das indústrias de processo)
portanto mesmo que todas as fábricas novas adotassem
um único padrão, seria insignificante perante a situação
atual de fragmentação do mercado entre vários protocolos de campo. Quanto a adoção dos novos conceitos
de cloud computing, virtualization etc, estes serão abraçados e incorporados nas arquiteturas dos sistemas de
controle com a mesma velocidade que apareçam. Rapidamente encontraremos formas de garantir que não
prejudiquem a segurança dos sistemas. O mercado não
vai esperar alguém “padronizar” a sua utilização. Dessa vez haverá uma adoção rápida das tecnologias ditas de
uso comercial com as considerações imprescindíveis da
nossa indústria de segurança nos dias de hoje. Estou
muito mais preocupado com o cyber terrorismo e a possibilidade de
transformar uma planta industrial
numa área densamente populada
num “political statement” do que
se Profibus é melhor que Fieldbus”, resume fortemente o sentimento comum sobre o tema Jim
Aliperti, Petrobras Account Director da UOP no Brasil.
Momento de transição
Pablo Fava, diretor de automação da Siemens, ressalta que o
momento é de modernização dos
sistemas de automação legados
concomitantemente à integração
de novos sistemas de automação,
principalmente num cenário econômico onde projetos green fields
estão cada vez mais escassos e os
clientes finais se vêem obrigados
aumentar suas produções utilizando o mesmo parque
fabril de 10, 20 e até 30 anos atrás. “É fato que muitas
plantas ainda utilizam troca de dados através de sinais
convencionais (4-20mA, 0..10V, sinais digitais, etc), da
mesma forma que algumas plantas foram inovadoras
mesmo nas décadas de 80 e 90. Independente do cenário, essas plantas vivem alguns dilemas sobre como
maximizar a produção sem que seja necessário substituir todo sistema automação existente? Ou como integrar novos módulos de automação com os sistemas
legados? E ainda como estar apto aos novos padrões
de produção e tecnologias que vão dominar automação
industrial no futuro? ”.
“Sobre a utilização de Ethernet na indústria, é claro
que o Internet of Things acabará chegando também na
área de controle de processos. Mas precisamos tomar
muito cuidado com a generalização. Tenho participado
de desenvolvimento de produtos na área de instrumentação por mais de 30 anos, incluindo desenvolvimentos
em Hart, Fieldbus, Profibus PA e WirelessHart; e até
no desenvolvimento de um transmissor de pressão com
comunicação via Ethernet, acredito que a Ethernet nos
instrumentos de campo só se justifica para dispositivos
muito complexos. Existem vários problemas técnicos,
econômicos, administrativos e com segurança e que
precisam ser resolvidos. Para começar, instrumentos
podem ser instalados em área classificada, o que limita
tensão e corrente que eles podem receber, e quanto
maior a velocidade da rede de comunicação, maior é
a energia requerida. As distâncias entre instrumentos e
sistema de controle podem ser bastante longas e como
sabemos, o cabo de Ethernet a 10 mbits/s não pode ultrapassar 100 m. Pode-se reduzir a velocidade para ganhar maiores distâncias, mas isso traz outros desafios.
Pode-se usar repetidores ou chaves, mas aí a instalação
se torna mais complexa, menos confiável e mais cara.
Instrumentos são normalmente instalados em atmosferas corrosivas, com alta variação de temperatura e
sujeitos a vibração. Trocar os dois fios de instrumentos
4-20, Fieldbus ou Profibus PA por quatro ou mais fios
para Ethernet requer uma boa justificativa econômica.
Aqui nos Estados Unidos e em alguns países da Europa existem muitas plantas com pessoal sindicalizado.
Estes sindicatos requerem que trabalho com Ethernet
seja feito por pessoal de TI, mais caros e menos disponíveis. Alimentação pela Ethernet reduz o número de
fios, mas isso também não vem sem desafios. Reduzir
a velocidade da rede permite maiores distâncias, mas
convém lembrar que a banda de transmissão em uma
linha multidrop diminui drasticamente com o número
de instrumentos. Estes são apenas alguns dos problemas. Tenho certeza que todos eles são solucionáveis,
mas a relação custo-benefício deveria poder justificar
este tipo de desenvolvimento e a maioria dos principais fabricantes de instrumentos ainda não encontrou
esta justificativa, exceto para alguns instrumentos mais
complexos que já utilizam alimentação separada da comunicação, e instrumentos a quatro fios. E não podemos esquecer que as razões que têm limitado a adoção
de comunicação digital continuarão existindo, até que
haja uma mudança de cultura. Vale a pena lembrar que
várias empresas de grande porte observaram ganhos
significativos depois que implantaram programas para
realmente tirar vantagens dos benefícios de Fieldbus e
Hart durante instalação, comissionamento e operação.
Mas isso não sepulta a Internet of Things, mesmo que
ela se limite a uma Intranet of Things por razões de
segurança. O que já está acontecendo é ter a Ethernet com fios ou fibra ótica conectando o sistema de
controle à gateways para redes wireless e às estações
remotas com entradas e saídas via Fieldbus, Hart, 4-20
mA ou Profibus. WirelessHart tem os instrumentos wireless comunicando através de mensagens cabeçalhos
curtos com a gateway, que comunica com o sistema
de controle através de Ethernet com protocolo Hart IP,
por exemplo. Mas instrumentos de campo devem continuar por um bom tempo com os protocolos existentes, conectados a interfaces Ethernet”, comenta Mestre
Peluso.
As respostas não são simples de serem respondidas,
mas todas têm em comum a questão dos Padrões! Padrões de comunicação e padrões tecnológicos que foram desenvolvidos desde o primeiro momento levando
em conta as tecnologias dos sistemas legados, tendências para o futuro e uma transição suave dos sistemas
Controle & Instrumentação Nº 213 | 2015 45
legados para as novas tecnologias.
“A transição dos sistemas legados para as novas
tecnologias também esbarra na capacidade técnica das
equipes de manutenção, operação e engenharia em assimilar e aplicar as vantagens básicas das novas tecnologias, assim como explorar ao máximo os recursos simplesmente inexistentes em sistemas baseados em sinais
4..20mA e Hart”, ressalta Fava.
“Dessa forma, é fácil entender que muitos clientes
finais ainda utilizam tecnologias convencionais, assim
como muitos fornecedores proveem produtos para tais
tecnologias, todavia negligenciar os novos padrões de
automação, investindo e aplicando tecnologias convencionais pode ser um erro estratégico que inviabilizará
um crescimento sustentável e a própria competitividade
dos clientes finais num curto espaço de tempo. Dentro desse cenário o padrão Ethernet a cada dia mais se
comprova como o caminho a ser seguido e o protocolo
Profinet cada vez mais vem se colocando numa posição
de destaque como o backbone de
comunicação que permitirá elevados índices de produtividade,
disponibilidade e conectividade
em diferentes cenários industriais,
seja numa indústria de manufatura, seja numa planta de processo”,
diz Márcio dos Santos, engenheiro de aplicação da Siemens.
Robert Gries, presidente
da Associação Profibus & Profinet International (PI), afirma que
a entidade acompanha de perto
esse cenário, dando suporte incondicional ao desenvolvimento
do protocolo Profinet, de acordo
com as tendências previstas no Industry 4.0 e demandas peculiares
para cada tipo de indústria. “Além
disso, a PI trabalha de forma incisiva na capacitação das
equipes de automação, de forma que elas estejam aptas a migrar sistemas legados para o Profinet, maximizando o uso dos sistemas de controle industriais. Isso,
na indústria de processos porque na manufatura, os
protocolos ditos seriais ainda dominam a maioria das
aplicações. Dentre eles, o Profibus DP lidera de forma
ampla o parque instalado com cerca de 50 milhões de
nós instalados ao redor do mundo ao longo das últimas
décadas. Vale ressaltar que já existem cerca de 10 milhões de nós Profinet em funcionamento e a proporção
de nós Profibus versus nós Profinet está demonstrando
a maciça aceitação deste último pelo mercado industrial”, comenta Robert Gries.
Atualmente, a cada dois nós Profibus vendidos, é
vendido um nó Profinet e já se projeta atingir a relação
1:1 em 2016. Considerando o tempo de vida dos protocolos e considerando que cada vez mais nós Profinet
são vendidos em relação aos nós Profibus, é possível
traçar cenários nos quais em poucos anos teremos a
transição suave das redes Profibus para redes Profinet,
em consonância com as funções previstas no desenvolvimento do Profinet, uma evolução natural do Profibus
sob redes Ethernet e muito mais.
Virtualização e IIoT
O cenário parece mais tranquilo para o protocolo
de origem europeia. Mas outras variáveis entram nesse jogo: a virtualização, a IIoT – Industrial Internet of
Things, Indústria 4.0/Smart Industry, Cloud Computing,
Cybersecurity...
Marcilio Pongitori afirma que a IIoT ganha espaço
naturalmente. “A tecnologia vem conseguindo adeptos
junto aos fabricantes e usuários devido também a grande quantidade de desenvolvimento de soluções com
esta plataforma. Desta forma é uma tendência que deve
dominar o mercado no médio e longo prazo”.
A virtualização está nas camadas superiores e vem
“descendo”; é um caminho sem volta, as tecnologias
de virtualização trazem muitos benefícios que dão mais
segurança e melhor capacidade de processamento por
alocação de memória de forma otimizada, assim, quem
usa menos memória tem menos disponibilidade e que
usa mais lhe é disponibilizado no momento correto, melhorando com isto a performance dos processamentos.
“Deve-se observar que toda esta integração só é possível quando há a digitalização dos sistemas e equipamentos, fazendo-os comunicar por protocolos digitais
aonde os dados serão usados para se transformarem
em informações e em conhecimento. Neste caminho
é fundamental preocupar-se com a segurança da informação, pois após o surgimento do STUXNET o mundo
de automação não é mais o mesmo é preciso cuidar de
coisas que não tínhamos preocupações no passado. O
controle de processos nas indústrias está timidamente
inserido nos conceitos de virtualização e consequentemente em cloud, no entanto, já é observado alguns
servidores virtualizados (PIMS e MES por exemplo) e
algumas aplicações menos críticas em nuvem, mas é só
uma questão de tempo. É necessário conhecer as novas
tendências, estudá-las e tirar delas o que há de melhor,
com isto, buscar melhorar a nossa competitividade”,
comenta Ronaldo Ribeiro.
Larry O´Brien não vê a virtualização para aplicações de dispositivos. “No entanto, a virtualização pode
ser usada na engenharia de sistemas e processos de design para acelerar o tempo de conclusão do projeto. A
maioria das tarefas associadas com o projeto dos buses
de campo pode ser virtualizada e em seguida implantada no local. Mas nesse contexto virtual é preciso atentar para cibersegurança e como você está gerenciando
os dados de diagnóstico. Hart e FF oferecem vantagens
Cover Page
46 Nº 213 | 2015 Controle & Instrumentação
nesse ponto porque são construídos a partir do zero para
atender aos requisitos de automação de processos”.
Ambientes virtualizados são realidades incontestáveis em TI, sendo que as grandes vantagens de tais
sistemas são comprovadas através da redução de custo
de propriedade, manutenção e operação centralizada,
assim como independência de hardware nas soluções
de software. Pablo Fava ressalta que as mesmas vantagens podem e devem ser exploradas pelo mercado de
automação, porém considerando as peculiaridades dos
sistemas industriais. “Atualmente nem todos os fornecedores de solução utilizam e/ou permitem a utilização de
todos os cenários previstos num ambiente virtualizado,
da mesma forma que as equipes de manutenção ainda
não estão 100% preparadas para manter sistemas de
automação baseados em ambientes virtualizados. Somando-se os altos custos iniciais para se implementar
um sistema de virtualizado, é fácil entender os motivos
pelos quais muitas plantas industriais ainda não utilizam tal tipo de solução. Atualmente, muitos sistemas de
automação estão sendo virtualizados única e exclusivamente no sentido de dar-se continuidade em sistemas
de automação aos quais não é possível encontrar Hardware e Software compatíveis com os sistemas legados
(baseados em Windows NT, 2000, etc)”.
Inconteste também que a grande migração para
sistemas virtualizados na indústria ocorrerá quando os
fornecedores, equipes de manutenção, operação e TI
atuarem juntos no sentido de explorar todos os ganhos
e reduções de custos oriundos de ambientes virtualizados. Dependendo do tempo de aceitação dessa tecnologia, pode ser que os sistemas de automação migrem
das atuais plataformas para ambientes virtualizados nas
diversas formas de cloud.
Robert Gries ressalta que, para os protocolos de
comunicação desenvolvidos sob o padrão Ethernet,
como o protocolo Profinet, não faz diferença se o sistema de controle/supervisão está rodando num sistema
virtualizado ou não.
Para os executivos da Siemens, a aplicação prática dos conceitos Industry 4.0 é o fechamento de ouro,
onde todas as tecnologias são aplicadas em conjunto e
objetivando os mesmos ganhos como aumento exponencial de produtividade, sistemas de produção flexí-
veis e inteligentes, engenharias de produção e automa-
ção totalmente integradas, monitoramento dos sistemas
produtivos em tempo real, resultando em total transparência e rastreabilidade do que está sendo produzido,
como está sendo produzido, onde está sendo produzido e para quem está sendo produzido.
Tomé Guerra lembra que a virtualização tem sido
incentivada pelos fabricantes, porém tem sido mais
usada na camada superior onde transitam informações
de monitoração/gerenciamento, nas camadas de PIMS,
LIMS, MES, etc.. “Já na camada de controle tem começado a ser usada, mas recomendando-se o uso de
servidores virtuais com redundância pelo menos nos
serviços mais críticos de base de dados, gerenciamento
de alarmes, estações cliente, etc.”
“A virtualização é usada em automação no nível 3
e acima, no modelo ISA 95. Tecnicamente é possível
virtualizar redes Ethernet utilizadas nos níveis inferiores
nesse mesmo modelo (ISA 95), mas é necessário que
haja uma razão atraente de negócios para fazê-lo. No
longo prazo, acreditamos que isso possa ocorrer, mas
nada para agora. Sobre IIoT, a primeira coisa que eu
diria a levar em consideração seria o nível de conectividade IP que um projeto específico requer. Qual o limite
máximo de distância que seu sistema de automação e
seus sensores podem atingir com o Internet Protocol?
Isso é importante porque tanto as visões de IIoT como as
da Indústria 4.0 incluem de forma praticamente ubíqua
toda a comunicação em rede. Hoje, muitos fabricantes,
provavelmente a maioria deles, deliberadamente projetam suas redes para limitar diversos tipos de tráfego
na rede. Nestes sistemas futuros, o tráfego de rede será
muito mais diversificado e, assim, as redes terão de ser
mais cuidadosamente provisionadas, e gerenciadas, de
modo que uma determinada rede possa cumprir múltiplos requisitos”, comenta Harry Forbes.
Raul Groszmann acrescenta que os sistemas industriais estão migrando para cloud e, aos poucos, paradigmas como vulnerabilidade do link de comunicação e
disponibilidade estão sendo quebrados. “A virtualização
dos servidores de automação se torna parte fundamental
deste processo, no qual os benefícios são significativos.
Em alguns anos, a maioria dos sistemas de informação
relacionados a automação serão virtualizados. O mundo
como um todo está migrando para tecnologia IP, sistemas
do chão de fábrica serão virtualizados e estarão na nuvem,
as redes de comunicação serão unificadas e a presença de
dispositivos inteligentes que interagem em um ambiente
unificado aumentará significativamente. Levar em consideração a reestruturação da Infraestrutura de Rede é fundamental para aplicação dos conceitos de Indústria 4.0 e
Connected Enterprise, sendo a gestão eficiente do controle da informação uma parte vital do processo. A criação
de políticas de segurança e controle de acesso que, até
pouco tempo, eram de exclusividade do TI, se tornam
obrigatórios na Manufatura e Industria de Processo”.
A Indústria 4.0 se baseia em pilares como Big Data, Sistemas Computacionais Cibernéticos, Internet das Coisas Industriais, Máquinas e Processos Flexíveis. Nesse contexto
os protocolos de comunicação serão a espinha dorsal que
vai permitir a integração e o transporte das informações
necessárias para se chegar a ela. Caso não sejam utilizados sistemas de comunicação baseados em padrões abertos, não será possível integrar um número praticamente
ilimitado de sensores e sistemas de controle das indústrias
no futuro. |
|
Primeiro encontro global do Fieldcomm
(Hart+Foundation Fieldbus) |
|
 |
|
No final de 2014 a integração das atividades e a construção de uma única organização marcou a fundação do
FieldComm Group, que congrega hoje as extintas Hart Communication Foundation e a Fieldbus Foundation o Hart e
o Fieldbus Foundation. “A partir de1º de janeiro de 2015, o
FieldComm passou a ser o responsável pelos protocolos Hart
Hart e FoundationFoundation e, em sua estrutura organizacional existe um grupo ligado diretamente à diretoria que é o End
User Advisory Council (EUAC), algo como um Conselho Consultivo de Usuários Finais, que tem a missão de assessorar a diretoria executiva em suas decisões”, comenta o representante
oficial da Petrobras no EUAC, Miguel Borges, engenheiro de
equipamentos Senior do Cenpes/Petrobras e responsável pelo
Lead – Laboratório de Controle e Automação, Engenharia de
Aplicação e Desenvolvimento, um dos membros dessa seleta
equipe formada ainda por John Rezabeck, Chairman (Ashland),
B. R. Mehta (Reliance), Duncan Turner (Apache Corporation),
Herman Storey (Consultor), Hamad Balhareth (Saudi Aramco),
Sartoru Nonkawa Nunokawa (Misuzu Erie), Michael Stafford
(Canadian Natural Resources Limited) e Rong Gul (Shell).
Além da gestão dos protocolos Hart e Foundation, o FieldComm
também cuida do novo padrão de integração de instrumentos
de campo, o FDI - Field Device Integration, cujo desenvolvimento foi suportado pela OPC Foundation, FDT Group, Profibus & Profinet International e empresas como ABB, Emerson,
Endress+Hauser, Honeywell, Invensys, Yokogawa, Siemens.
Talon Petty, gerente de marketing e desenvolvimento de negócios do FieldComm Group, explica que a combinação de organizações FF e Hart é um movimento administrativo. Apenas as
organizações se fundiram, e não a tecnologias. “As tecnologias
são tão diferentes que não podem ser mescladas”, pontua Miguel Borges.
As principais vantagens dessa união administrativa são para
os membros das duas organizações pois elas são formadas pelas
mesmas empresas; então, unidas, os recursos são otimizados.
Segundo Talon, para os usuários, as vantagens não são imediatas. “A vantagem é que somos agora um padrão aberto mais forte para a comunidade e, portanto, podemos orientar a indústria
e apoiar a comunidade de usuários mais fortemente”.
Larry O’Brien, vice-presidente de pesquisa do ARC Advisory Group, acredita que o FieldComm traz benefícios tanto
para os usuários finais – que têm um único e forte grupo para
dar suporte para duas tecnologias - como para os fornecedores –
que terão custos reduzidos em termos de adesão e desenvolvimento.
Miguel Borges lembra ainda que a união propicia melhor
aproveitamento dos recursos e das sinergias, mas os protocolos
seguem independentes, bem como a iniciativa FDI, criada há
alguns anos e que estabeleceu que se extinguiria logo após a
primeira especificação. Talon explica que a especificação FDI
está completa e os fornecedores estão desenvolvendo seus produtos sob o ambiente de desenvolvimento integrado (IDE). O
FieldComm e a Profibus estão agora distribuindo as regras e registrando os produtos desenvolvidos para a especificação. Devemos começar a ver produtos no mercado em 2017 porque esses
esforços de desenvolvimento levam algum tempo. Os fornecedores vêem benefícios em termos de redução dos custos. Agora
apenas um pacote é necessário para cada dispositivo, para cada
protocolo; antes, os fornecedores tinham que desenvolver produtos que conformavam tanto EDDL quanto FDT.
“Agora quem gere o FDI é o Fieldcomm. E é bom lembrar
que o FDI se baseia no OPC UA, mais robusto e que independe
da plataforma que se utiliza. Ele está numa fase inicial e até existirem produtos no mercado vai levar um tempo. Uma iniciativa
do Fieldcomm que impacta já é o processo de usabilidade. O
Fieldcomm está investindo para tornar o FF tão simples quando
o 4-20mA”, diz Miguel Borges que pôde, durante a primeira
reunião do EUAC - que aconteceu no início de dezembro, em
Tokio, no Japão – perceber que os usuários do mundo inteiro
sentem as mesmas dificuldades.
Hoje, se o usuário precisa substituir um instrumento
FF, ele precisa realizar várias operações; não é um simples
plug&play. Mesmo versões mais antigas do mesmo fabricante
precisam ser engenheiradas. E um deslize pode impactar na
operação do segmento FF. “Aí entra o do FieldComm, que está
trabalhando em nova versão do ITK que irá facilitar em muito
a vida do usuário final Fieldcomm: o lançamento da nova versão do ITK (6.2) que permite substituição imediata mesmo de
versões diferentes dentro da mesma marca. Já é um começo
pois o mesmo modelo com o firmware revisado garante a compatibilidade com versões anteriores. E isso torna a utilização
do protocolo mais fácil”, afirma Miguel que adianta que outras
novidades devem ser lançadas pelo Fieldcomm ainda no primeiro semestre de 2016.
Vale ainda destacar a criação de dois grupos de trabalho
no FieldComm: um dedicado a desenvolvimentos voltados para
a utilização mais amigável dos protocolos, o Usability Working
Group, e o outro dedicado a desenvolvimentos na área de cybersecurity, o Cybersecurity Working Group. Por fim, o EUAC começará a revisar os engineering guidelines editados pela extinta
Fieldbus Foundation. |
|
|
|
|
|
|
|
|
LEIA MAIS
NA EDIÇÃO IMPRESSA |
|
DESEJANDO
MAIS INFORMAÇÕES: redacao@editoravalete.com.br
|
|
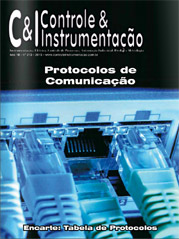 |
Clique na capa da revista para
ler a edição na íntegra |
|
|